
德国航空航天中心(DLR)为自己的工作单元开发了一个灵活的自动化平台,以构建CFRP航空结构系列,这些结构使用相同的过程-干燥的非卷曲织物,贴放叠层和树脂灌注-来制造后压舱壁和 机身面板。不教授协作机器人,而是定义它们自己的无碰撞路径,以根据CAD和过程定义输入以及AI算法将切层放置到工具中并将其放置到工具中。这种由AI驱动的自动化是未来智能Composites 4.0工厂的基础之一。
复合材料4.0是工业4.0宇宙中的一个小星系,工业4.0是产品和服务如何设计、生产、交付、操作、维护和退役的数字化转型。复合材料制造的目标是使用自动化、传感器和数据、5G通信、软件和其他不断发展的数字技术,使产品和流程更高效、更智能、更适应。
复合材料制造商正在沿着一个光谱进行这种数字化转型。初的步骤包括在线检查和优化过程,以减少浪费和成本,同时提高零件质量和产量。更先进的解决方案致力于智能化、自主化的生产,这不仅是敏捷的,而且能够响应甚至预测不断变化的市场和客户需求。
“复合材料4.0不是终点,而是一种工具,”德国亚琛工业大学AZL Aachen轻质集成生产中心常务董事Michael Emonts博士解释道。他的iComposite 4.0项目展示了一种自适应过程链,有可能将汽车底盘成本降低50-64%
复合材料部件制造商Dynexa(德国Laudenbach)的总经理Christian Koppenberg认为:“仅仅是数字化与数字化转型是有区别的。数字化转型实际上改变了企业背后的流程,并开启了新的机遇和商业模式。”
“复合材料4.0不仅使用机器人,”德国航空航天中心(DLR)轻量化生产技术中心(Augsburg的ZLP)负责人Michael Kupke博士断言,该中心开发了配备有人工智能[AI]的工作单元 在这里,协作机器人可以从生产复合后压舱壁切换到机身面板,而无需重新编程或重新训练。“这项技术可确保您不必教机器人,因为这没有商业理由。复合材料4.0不仅可以提高效率和削减成本。公司如何思考和处理生产方式的变化将决定哪些公司能够生存,哪些公司不能生存。”
自适应预成型:RTM
“复合材料 4.0项目的想法是通过结合干燥的、长玻璃纤维(25-30毫米)的喷射,然后通过自动纤维放置(AFP)用单向碳纤维网格加固,从成本效益高的碎片和拖块中创建预制件,”Emonts解释说。“所选择的样板机,在汽车底板下方,之前是用更昂贵的纺织品制造的,这也造成了60%以上的浪费。”
复合材料4.0转换需要集成的纤维喷涂、纤维沉积和随后的树脂传递模塑(RTM)工艺,这样他们对彼此的反应和适应基于步骤之间的质量测量部分(图1)。“我们使用机器视觉系统从Apodius GmbH(德国亚琛)与光学激光传感器和摄像头模块描述的表面拓扑喷预成型,“Emonts说。Apodius对该软件进行了改进,以分析各个方向的纤维百分比。iComposite 4.0线比较这与数字设计,并决定是否满足机械要求。如果是,则采用标准的UD网格进行加固。如果没有,它决定在哪里放置额外的UD纤维层。
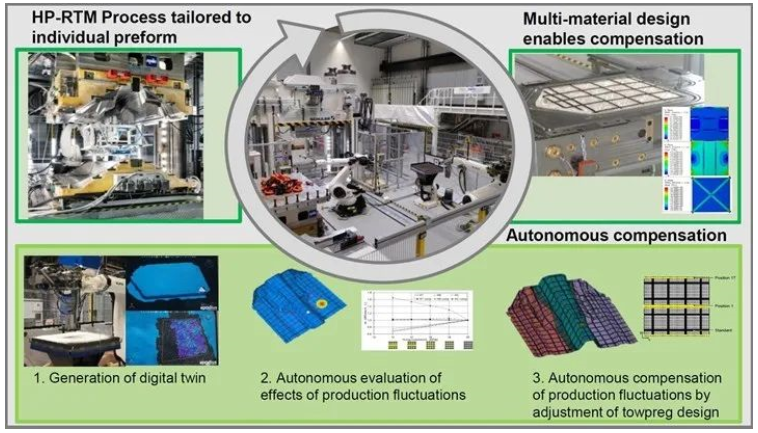
该AZL Aachen led项目将3D纤维喷涂、自动UD胶带铺设和RTM结合到一个自适应的工艺链中。自动化允许流程基于彼此作出反应
对预成型质量的影响,采用激光技术对预成型质量进行评价。来源| AZL Aachen
但是,这些额外的UD层可能导致零件厚度和几何形状超出公差。他解释说:“因此,我们将预成型线与自适应RTM工艺相结合,必要时可通过增加压力机某些零件上的压力来调节零件厚度。” 这也是自动化的,目的是代替生产线操作员的干预,但是它确实需要使用测量数据和标准FEA软件模拟零件性能。
“目前,零件力学性能的模拟是离线进行的,”Emonts说。“我们生成了一个过程和部件变化的数据库,创建了算法来对每个变化做出反应,并通过FEA验证这些变化。因此,基于由线测量的变化,算法指导它执行适当的缓解。为了使这条线能够原位自适应,下一步将是增加机器学习。与此同时,AZL正在进行多个复合4.0项目,包括自优化混合热塑性复合材料的生产,以及带有基于带的定制坯料的集成加劲的注塑件。
零缺点碳纤维增强塑料机翼皮
ZAero项目是另一个重要的复合材料 4.0项目,于2016年启动。该项目旨在提高大型碳纤维增强塑料(CFRP)结构(如机翼皮)的生产率。通过使用预浸料AFP或Danobat(西班牙Elgoibar)的自动干材料放置(ADMP,请参见“证明干织物的可行性,用于大型飞机结构的灌注”),可以通过自动在线检查来减少缺陷。树脂灌注或预浸料固化过程中的过程监控将预测固化状态并缩短周期时间。收集的过程和缺陷数据与FEA一起用于预测零件性能。然后将其输入到决策支持工具中,以解决已发现的缺陷。开发了用于CFRP机翼皮的零件流模拟,将其输入该工具后,有助于优化返工策略(图2)。如今,许多这样的零件在制造过程中进行了返工,但仅在NDI之后才进行返工。更早的返工和改进的工艺控制确实是ZAero项目的目标,也是其实现生产率提高15%,降低15-20%的目标的推动力生产成本和浪费减少了50%。
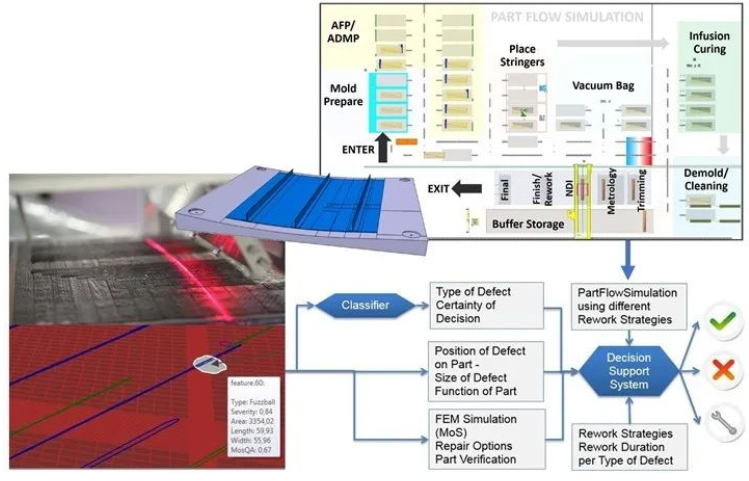
ZAero项目展示了CFRP加筋板的在线缺陷控制。从左上方逆时针显示:集成了AFP的激光传感器,缺陷分类,流程图,显示了与零件性能和决策支持工具的FEA建模相结合以及CFRP机翼蒙皮的零件流程模拟(右上),以优化返工策略 。
通过2019年9月的终审查,由项目负责人Profactor(奥地利施泰尔(Steyr,Austria))开发的预浸料AFP传感器不仅实现了自动化在线检测,而且还可以用于现场校正零件。“该传感器可以检测标准缺陷,例如缝隙,重叠,FOD,绒毛和扭曲的丝束,以及每个丝束的早晚切割”,Profactor机器视觉负责人Christian Eitzinger博士说。丢失的丝束可以通过将另外的丝束精确地放置在省略的位置来自动纠正。但是,必须停止机器以清除绒毛或扭曲的丝束。“使用DassaultSystèmes(法国巴黎)的3D Experience for CATIA建立的数据库,我们可以根据缺陷的大小,形状和类型来计算对零件性能的影响。处理层中的所有缺陷仅需几秒钟。然后,机器操作员决定可以保留哪些缺陷以及必须进行哪些修复。”
对于输注过程的监视和控制,空中客车公司(法国图卢兹)通过子公司InFactory Solutions(德国陶克基兴)开发了三个传感器,用于测量温度,固化状态和树脂流动前沿。“我们已经将它们与CATIA 3D Experience集成在一起,并表明可以可靠地获取数据并将其添加到每个零件的数字线程中,” Eitzinger说。
演示者的后三个部分是带有三个纵梁的上翼子板小节。对于这一部分,Profactor的决策支持工具在合作伙伴FIDAMC(西班牙马德里)进行了现场演示,该工具已与基于Siemens PLM(美国德克萨斯州普莱诺)Tecnomatix Plant Simulation软件的零件流模拟相连接,并在奥地利的Profactor服务器上运行。除了建立缺陷数据库外,ZAero还进行了机器学习实验。手动设计的生成计算机模型与深度神经网络相结合,对缺陷进行了检测和分类,即使在人为创建的缺陷数据存在的情况下,也可以在真实的ADMP监测数据中对不同区域(间隙,重叠,拖曳,毛刺球)的正确分类率达到95%用于深度网络培训(类似于如何在一系列故意缺陷上校准超声测试系统)。
“我们一定会追求某种下一阶段的成果,” Eitzinger说。同时,Profactor正在将模块化传感器商业化,以解决自动铺网过程中的纤维取向和缺陷。InFactory Solutions还提供其AFP和树脂注入传感器,光纤放置合作伙伴Danobat和MTorres(西班牙纳瓦拉的Torres de Elorz的Torres de Elorz)现在正在销售带集成在线检测的设备。
Dynexa的数字化转型之旅
Dynexa是一家复合材料零件制造商,专门研究CFRP管和轴。“我们一直试图将一切数字化。”常务董事科彭贝格说。“我们已经摆脱了手动和模拟流程,主要将所有内容集成到我们的ERP [企业资源计划]系统中。但是我们如何在制造业中做到这一点?我们了解到,我们在工作程序协议或过程中放入的所有内容都是代码,这是数字转换的基础。但是它存储在哪里?在本地服务器上,在云中还是在计算机中?我们将问五个人,并就应采取的措施得到七个答案。”
幸运的是,德国政府已经为大学制定了一项计划,为中小企业(SME)提供免费的工业4.0咨询。Dynexa开始与达姆施塔特“ Mittelstand(SME)4.0”能力中心合作。Koppenberg回忆说:“他们说不用担心数字架构,而更多地关注需要测量的内容以及如何做到这一点。” “我们选择了一个涉及大量人工测量的过程,我们知道我们遇到了质量,时间和成本问题。”
Dynexa使用湿丝缠绕工艺。” 关键步骤是树脂拾取,其中将干纤维运行到压实辊上,该压实辊从树脂浴中滚出。刮刀紧靠压实辊,该刮刀确定在缠绕前要与干丝结合的树脂量。Koppenberg说:“如果收集的树脂太多,我们可能会超过指定的管子直径,但是如果树脂过多,我们就有可能跌落到允许的小直径以下。”
他指出:“如果不进行测量,则只有在所有价值都投入后,您才知道固化后的终直径。” “因此,操作员必须停止机器,测量零件,写下来然后重新启动。根据多年的经验,我们知道在缠绕的每个阶段层压板的厚度应该是多少。因此,操作员可以比较测量结果,并根据需要调整刮墨刀以校正树脂的拾取,但这非常手动,并且需要操作员的技能和经验。”
Dynexa与Darmstadt SME 4.0能力中心合作,开发了一种数码相机系统,用于监控管/轴的厚度,并在纤维缠绕过程中自动调整树脂取料(底部)(顶部),从而消除了人工测量,提高了效率和成本。
为了对此进行数字化,Dynexa与无数激光和相机制造商进行了交谈。“他们会说,‘我们有解决方案’,但是没人能使它奏效,”科本伯格指出。但是,达姆施塔特大学(University of Darmstadt)团队通过确定由于某些物理因素(例如从潮湿表面反射的光)而需要进行的校正,从而启用了摄像机的使用。他补充说:“现在,我们已经将绕线机连接到测量设备,该设备以非常标准化的方式运行。”
该团队开发了校正表和决策算法的数据库,该数据库使细丝缠绕机能够知道要缠绕的特定管子的每个阶段的目标。Koppenberg解释说:“如果测量设备的输入显示树脂拾取量不在应有的位置,则长丝缠绕机会通过调整刮刀将其恢复到规格状态,而不会停止缠绕以进行测量。”
现在,每台绕线机都有数字测量系统和一个以太网卡。“昂贵的部分是安装和运行到服务器的电缆,”科彭伯格打趣道,“但是现在我们可以与每台机器通信并收集所有数据。”还有另一个好处。“以前,操作员是在机器上进行编程的,但是一旦将它们连接到服务器,我们就可以在任何台式机或便携式计算机上进行编程。这进一步减少了停机时间,并消除了另一个生产瓶颈。”
数字化的步使Dynexa改善了过程控制,质量和效率,使其更具成本效益。它也刺激了进一步的转型。
改变复合材料的范例
空降飞机公司(荷兰海牙)于2019年9月启动了针对自己供应商的按需制造平台,用于复合材料的自动化制造。供应商可以使用该工具将设计输入基于Web的平台。然后,系统即时创建机器代码,并确定生产持续时间和成本。然后可以对产品进行定制,并在订购后在自动化生产单元中进行生产。该平台是使用机载自动层压单元(ALC)来处理热固性预浸料的。它将扩展到其他过程,例如,为SABIC(沙特阿拉伯利雅得)特种产品业务部门开发的大批量热塑性复合材料(TPC)生产线。
Airborne于2019年启动了其复合材料在线平台,客户可以在其中输入设计并接收Airborne自动化制造单元生产的层压板/零件的成本并估计交付时间,其中包括在未来的扩展中开发的Falcon大批量热塑性复合材料生产线 SABIC(底部)。
“该平台是我们如何看待复合材料制造的数字化未来的关键要素,”空降公司席技术官Marcus Kremers说。“五年前,我们从零件制造业务模式转变为帮助客户实现自动化和数字化。我们正在开发一系列解决方案,以使客户可以轻松地使用复合材料进行建造。”该产品组合包括ALC,自动蜂巢灌封,自动铺板套件以及使用TPC胶带的大批量生产线,SABIC将其称为Digital Composites Manufacturing Line(DCML),而Airborne称为Falcon。后者是空降定制解决方案的一个例子。克雷默斯说:“我们将复合材料和零件的制造知识嵌入到这些自动化系统中,从而使客户不必成为专家。”
机载有三种商业模式:购买自动化设备,租用或出租给机载,以通过制造即服务(MaaS)进行运营。机载自动化单元具有传感器和在线检查系统,它们可以根据客户定义的缺陷和公差数据库生成警报。“猎鹰产品线对视觉质量缺陷的容忍度很低,” Kremers指出,“但我们的航空航天自动化更多地受到结构容限的驱动。我们还不断提高技术的自学习能力和自适应能力。例如,我们用于ALC胶带铺设的下一个软件版本将具有识别缺陷和即时修改生产程序的能力。”
从长远来看,愿景是扩展按需平台,以收集分布在多个公司和地区的复合零件生产能力。Kremers引用了Protolabs(美国明尼苏达州Maple Plains),该公司可在短短一天之内按需提供注塑成型,钣金,CNC加工或3D打印的原型。同样,Plyable的在线应用程序(英国牛津)提供制造复合材料的模具,提供从聚氨酯板到复合材料,包括碳纤维材料和3D打印工具。“这是组织价值链的另一种方式,” Kremers说。“我们正在制造使复合材料零件成为可能的机器和软件。”
AZL亚琛公司还通过其超快速固结机来实现这一目标,该机用于在不到五秒钟的时间内生产多层TPC层压板。它在2019年实现了商业化,使用了Conbility(德国亚琛)机器人自动激光辅助AFP涂布器和25毫米宽的UD胶带,以及分条流原理(这是高速印刷行业中的新技术)可以生产各种厚度的简单地钉或完全固结的TPC层压板,并带有局部增强材料。“我们的愿景是提供可扩展的机器,以支持在线平台,” Emonts说。“生产线可以有多个工作站,每个工作站都有多个AFP涂布器。客户将输入要求,并获得有关活页簿,成本和交付的选项。终确定后,施用者彼此沟通以组织生产,而不是操作员。这是定制复合材料的完全智能生产。”
自动化!自动化!
ZLP的主要重点是CFRP结构的自动化生产。ZLP灵活自动化团队负责人Florian Krebs指出:“很难证明只有一个零件或程序实现自动化。” “但是,如果您从特定于任务的机器转移到几乎无需额外设置即可重新配置的自动化平台,那么您现在有了一个业务解决方案。平台越灵活,投资回报就越快。”
开头图像中显示的工作单元是ZLP项目PROTEC NSR的一部分,旨在按照相同的工艺路线制造一系列零件:干式非卷曲织物的拾取和放置叠层以及树脂灌注。“这个过程是为空客A350后压舱壁设计的,但是您也可以在这条生产线上制造机身面板或机翼罩,因为步骤很相似,” Krebs说。
“要实现灵活的自动化平台,需要某些技术基础,包括机器人的算法,传感器以及如何理解它们产生的数据,” Kupke说。“例如,PROTEC NSR生产线的设计朝着大的模块化方向—所有模块相互互连,以展示一种可自我配置,校正和优化的系统,可扩展的尺寸和复杂性。”
图5.灵活智能自动化的数字结构
对于PROTEC NSR项目,ZLP开发了一个灵活的自动化平台,该平台可以生产CFRP后压力隔板(右上)或机身面板(右下),并可以通过简单地更改CAD文件在这些之间快速切换。工具链中的工程师定义的说明(深蓝色框)控制着如何解释CAD数据以自动生成新的工艺步骤。
他解释了自己的模块,包括CAD模型,过程定义,允许对过程进行仿真和执行的过程模型,制造执行模块,用于获取数据的传感器,用于注释数据的软件以及用于存储的数据库。
“在模块左侧,您制定了一个计划。然后执行模块将执行该计划。” Kupke说。“在过程步骤中,我们从所有涉及的机器和过程中获取数据,例如切割机,机器人,建筑物(温度,压力,湿度),取放期间的摄像机等。我们分析数据在处理过程中实时进行,并且还会自动使用元数据注释收集的数据,以将其馈送到数据库中,这构成了处理过程中数字孪生的基础。数字双胞胎重要的一点是拥有一个存储库,是一个真理来源。每个零件的CAD模型和流程定义都是其唯一真实性的一部分。”
安装了这些模块后,只需按一下按钮,生产线就可以自主运行。机器人从CAD模型,生产计划和摄像机中推断出接下来要切割的工件,并在桌子上寻找工件(例如,从其他100个工件中查找)。“他们决定如何配置夹持器以将其拾取并放置在工具中,并知道将其放置在何处。”机器人根据生产计划确定所有过程步骤的每个开始/结束路径,并知道何时完成。“通常,这些路径是由人教的,”库普克指出。“但是在我们的系统中,每条路径都是自动定义的,不会发生碰撞,而且是实时的。如果更改CAD模型或过程定义,则机器人将进行调整,而无需任何额外的教学工作。但是,如果您完全更改零件怎么办?使用这种类型的自动化,您可以非常快速地进行更改。这是实现灵活生产的途径。我们在ZLP的作用是通过开发技术砖并将它们联系在一起来铺平这条道路。”
机会与本体
COVID-19大流行突出了灵活生产的价值。它还创造了越来越不可预测的商业环境。“在过去的两到三年中,一切都变得更加动荡不安,” Dynexa的布鲁克(Bruckhoff)说。“我们的客户非常想要快速的答案,以便响应他们的客户。通过提供新的在线生态系统,我们使整个供应链更具竞争力。”
这是航空业公认的。“我们需要数字化的生产线和整个站点的基础,以实现水平和垂直整合,” VDI航空技术部技术部主席马克·菲特(Marc Fette)说-德国工程师协会和复合技术中心(CTC)空客的R&T子公司。Composites 4.0中的CTC项目包括物料和资产跟踪,协作机器人,高级流程链等。但是Fette强调了对本体的需求—本体是数字通信和数据交换的术语和通用协议。(请参见在线侧栏“ Composites 4.0体系结构和本体”。)
他解释说:“您需要给定工厂中所有机器和生产系统的整体网络,但这也必须扩展到整个价值创造链,包括工程,采购,物流和材料以及过程认证等学科, 一方面。另一方面,必须考虑所有利益相关者,例如供应商,并使其参与此变更过程。我们看到了许多试点项目,但是当您详细查看时,仍然缺少针对每个公司或生产链采用整体方法的策略。”
他继续说:“我们拥有庞大的供应商网络,他们具有相同的要求才能作为数字化供应链运作。我们的大多数供应商都是为飞机制造商(空客和波音)服务的中小型企业。如果没有关于通用标准的讨论,则可以将这些挑战传递给供应商。他们很可能无法负担所有机器的两组不同标准,包括文档,评估数据,网络安全性等。”
Fette承认这些想法很重要,并表示飞机原始设备制造商正在制定应对这些挑战的计划。“但是这样的障碍很多,而且确实很复杂,不仅涉及技术,还涉及社会,经济,人机工程学和法律问题,这是一个思想上的变革过程。我们才刚刚开始。但是要取得成功,我们必须理解,这些新系统依赖于人员,而且这些人员必须参与其中,不仅是原始设备制造商,还包括整个网络。”
ZLP的Krebs指出:“各行各业的市场变得越来越分散,每个人都面临着转型与转变。” ZLP的库普克(Kupke)补充说:“许多人并不认为这是一个机会。”但是那些确实看到这个机会的人预见到了实现由Composites 4.0启用的Composites个性化的访问,因此,市场变得更加广阔,包括我们才刚刚开始构思的应用程序。