随着环境意识的提高,如图1所示,欧洲、美国和亚洲等正在考虑引入二氧化碳排放法规或燃油效率法规。在严苛的欧洲,2020年已决定将二氧化碳排放量限制在95克/公里以下,并且正在考虑将来引入更严格的限制。美国部分地区有强制供应一定比例以上环保车的举措,在亚洲也在讨论相关措施,预计未来这一举措将进一步加速。如图2所示,每种动力总成的单位距离CO2排放量与车辆重量之间的关系,很明显它们之间存在很强的相关性。从该曲线的斜率来看,车体重量减轻100公斤可以减少20g/km的CO2的排放。也就是说,车辆的轻量化是减少CO2排放的有效方法。
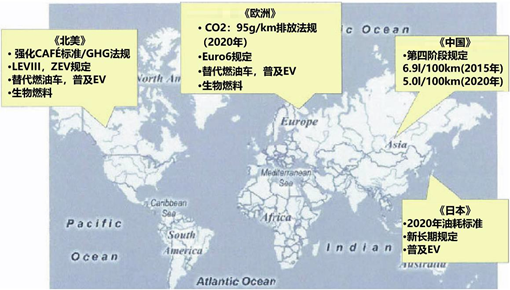
图 1 汽车排放限制及油耗限制动向
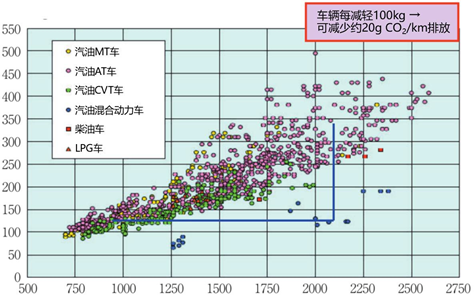
图 2 CO2排放量与车辆重量的关系
2. 汽车的轻量化案例及 CFRP 应用于汽车的基准版车型
在上述背景下,各地的汽车制造商都在开发以轻量化为主要目的的车型。这里着重阐述一下采用CFRP的两个实际应用案例。在量产车中大量使用CFRP的趋势日益增长的今天,德国BMW的电动汽车i3成为大家热议的话题。
如图3所示CFRP的应用说明。为了控制重量,车体使用了约100公斤的CFRP,这在量产乘用车中并不常见。车身的上下壳体是采用环氧树脂的高速RTM工艺成型,用弹性体粘合剂粘合,并将其在铝制底盘通过几个点的结合制造而成。RTM的固化虽然没有达到100℃、5分钟的目标,但实现了非常高速的固化。CFRP的供应链很是复杂的,使用的碳纤维前体是日本厂家提供的,纤维在美国碳化后在德国完成织物,碳纤维碳化所需的电力从便宜的地方调配。虽然它具有电动汽车的特性,但可以说已经确立了一种应用CFRP的理念和方法。
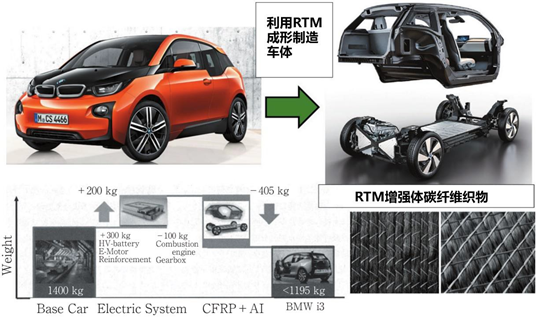
图 3 BMW 推出的电动汽车 i3(CFRP车体)
另一个案例是丰田汽车公司开发的雷克萨斯LFA,作为日本开发的一款实验性跑车,引起了大家的关注。图4展示了驾驶室采用CFRP的各个部件和相对应的技术。似乎有意尝试了各种技术,例如与飞机几乎相同的预浸成型、SMC、以及将树脂压入干织物的RTM等。该车限量生产500辆后停产。
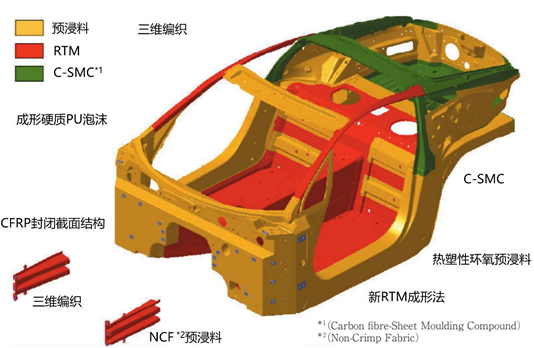
图 4 丰田汽车开发的雷克萨斯 LFA 中使用 CFRP的部品和技术
3.CFRP 成型技术应用于汽车的前景
从目前CFRP在汽车上的应用现状来看,目前CFRP的成本仍然很高,因此除了部分跑车和F1赛车外,其在量产乘用车上的应用还处于起步阶段。不过,主要厂商的研发动力强劲,特别是今后面向量产车的结构部件依次投放市场的动向将加速,其中CFRTP的应用研究在欧洲非常活跃。
作为讨论CFRP在汽车中应用的前提,我们将对CFRP成型技术从飞机到汽车再到通用机械零部件进行全面概述。图5是整个CFRP成型技术的路线图。在飞机的情况下,我们强调以高强度和高刚性为代表的机械性能,并且由于生产零件的数量少,并完成了一项用高压釜这种自动釜对使用连续纤维、热固化树脂的预浸料进行加热固化的技术。因此,作为一种适合稍微提高生产速度的技术,如i3中所述,在完全封闭的阴模中填充碳纤维织物等强化体,注入含有固化剂的树脂,使其尽快固化,即Resin Transfer Molding(RTM)技术。图中左下方向是一种快速成型CFRP的技术,以小齿轮、个人电脑等一般机械零件的情况为例,将含有非常短的碳纤维的热塑性树脂颗粒熔融、注射成型的技术。该图的左下方是一种非常快成型CFRP的技术,以一般机械零件,例如小型齿轮和电脑的壳体为例,将含有非常短的碳纤维的热塑性树脂颗粒熔融、注射成型的技术。由于汽车结构部件的许多部分都需要强度,因此开发了与比注塑成型长的纤维和热塑性树脂混合进行冲压成型的技术。这个代表性例子将在后续章节中叙述。
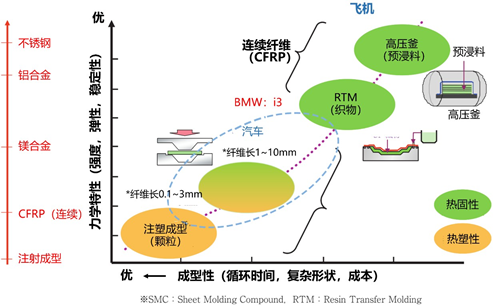
图 5 CFRP 成型技术与力学特性的关系
如图6所示,核心技术LFT-D挤出材料的制造方法概念图。热塑性树脂原料和添加剂的混合物先被熔化并捏合到下一个螺杆轴中,由连续碳纤维束供给的碳纤维束通过与螺杆的碰撞或树脂的剪切场中被切断,并在树脂中剪切力的作用下进行混配。因此很难准确控制纤维的长度,本质上会产生纤维长度的分布。纤维长度的决定因素包括螺杆的转速、纤维·树脂的供给量、搅拌装置内滞留时间、树脂混配时的压力·温度等,这些因素相互之间存在着复杂的影响。碳纤维的长度与所得成型物的力学性能密切相关,除了静态弹性模量和强度之外,冲击特性也很重要,特别是为了维持冲击强度,需要一定长度以上的纤维。
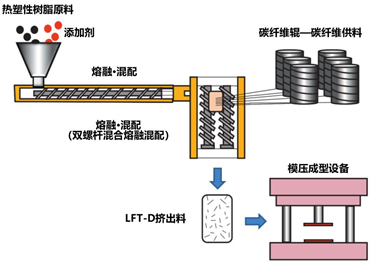
图 6 LFT-D(Long Fiber Thermoplasitic-Direct)的核心—混配体的挤压·制造
未来应用于汽车的 CFRP 成型技术趋势是以 LFT-D 为代表的热塑性树脂/不 连续纤维型 CFRP,以及高压/高速 RTM 与连续碳纤维相结合的 CFRP 应用方向, 预计将根据每种车型的生产速度、零件等扩大应用范围。在热塑性树脂/非连续 纤维型 CFRP 的情况下,假设强度和刚性可能不足,在这种情况下,可以考虑使 用热塑性树脂/连续纤维型 CFRP 增强 LFT-D 的应用。图 7 是 JEC 展会上荷兰Tencate公司出展的采用Tailored LFT-D 工艺生产的汽车零部件的照片。这是 采用德国Fraunhofer 研究机构的 LFT-D 技术,以织物强化热塑 CFRP 为表皮,以 LFT-D 材料为核心的一种夹层材料,弥补了 LFT-D 的强度和刚性不足的问题。这个方法代表将来的一个技术发展方向。
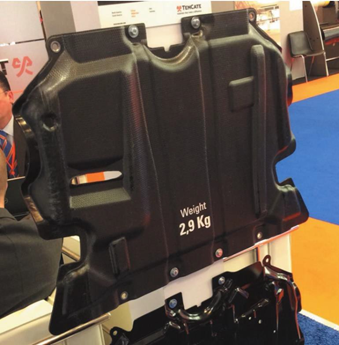
图 7 荷兰 Tencate公司利用 Tailored LFT-D工艺生产的汽车部件
4.名古屋大学复合材料中心(NCC)在汽车用 CFRTP 上的研究
为了应对的发展趋势,名古屋大学NCC在经济产业省直接资助的基础上,从2013年起开始,与东京大学共同启动了致力于用于汽车结构的热塑性CFRTP(Carbon Fiber Reinforced Thermo-Plastic)、结构设计和加工技术的研发。2014年,合作架构发生了一些变化,变成了以NEDO为龙头,经由新设立的“新结构材料技术研究组合(ISMA)”投入项目资金的结构。
在这样的框架下,在名古屋大学NCC开始着手以较少的零件数量、能够降低成本的技术来制造车身(底盘)的研发为目的,在量产车上使用CFRTP。
具体来说,通过引入现有的铝合金制基础车型,设计一个与它几乎相等刚度的车身结构,适当地分割和生产,进行接合、组装构成底盘。作为量产这种底板和侧壁结构的成型技术,考虑采用LFT-D技术。该项目的目标及要点如图8所示。
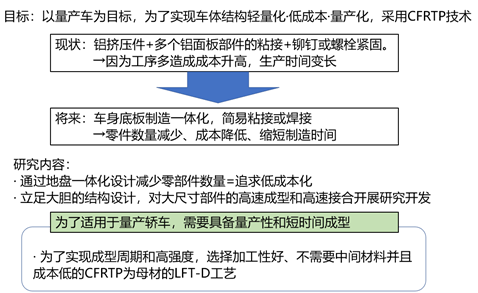
图 8 名古屋大学 NCC 实施的项目目标概要
通过实施该项目,认识到LFT-D成型技术需要克服以下一些关键要素。
(1)由于基体树脂在熔点附近暴露在大气中一段时间是不可避免的,因此需要提 高树脂的抗氧化性。
(2)掌握保持碳纤维长度的技术诀窍与充分使纤维分散之间存在二律背反的关系。
(3)为了保持LFT-D混炼体的良好流动性,需要对其进行适当的温度管理。
(4)确立LFT-D混炼体高速供给和定位的物料搬运技术。
(5)尽可能缩短LFT-D混炼体从挤出到压制成型之间的时间。
为了确保冲击强度,需要保留一定长度的纤维,但如果试图保持纤维长度,则很有可能会受到混炼条件等的限制,在认识到二律背反同时,设定合适的长度目标是技术发展的核心之一。
通过对这些技术课题的认识和改进,当时遇到的一个难题,即高质量平板成形问题通过引入了热风循环炉的保温系统得以顺利解决。此外,通过进行这些技术改进,还可以确保良好的流动性,并且可以在内部形成格子网状的型材(图9)。特别是左图所示,具有高扭转刚度的格子状网的型材,必须利用LFT-D技术才能生产出来,这也预示着该技术发展具有广泛的应用前景。
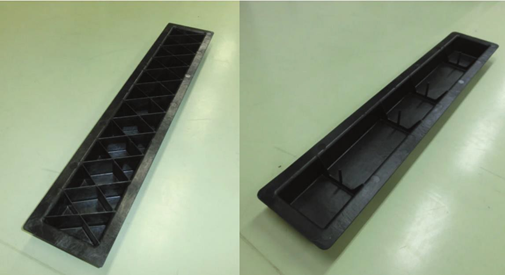
图 9 必须利用 LFT-D 成型技术完成的增强型材
(左:45°格子状 右:90°格子状)
此外,如前文所述,欧洲开发了一种以LFT-D为芯材,热塑性树脂编织预浸料为表面材料的三明治结构。与此同时,NCC成功研制了与图7不同结构的热塑性预浸料的混合成型部件,它使用碳纤维芯材的LFT-D、表面材料采用碳纤维织物作为增强材料。图10、图11展示了在不同形状成型的示例。
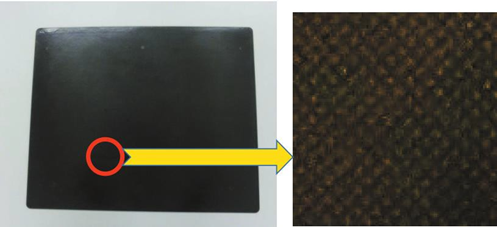
图10 碳纤维织物表面材料/LFT-D 芯材的 CFRTP 混合平板的成形例 表面材料:3K 线碳纤维平织 1ply,母材全部为 PA6
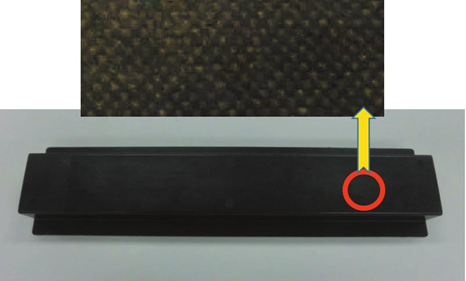
图11 碳纤维织物表面材料/LFT-D 芯材的 CFRTP 帽形的成型例 表面材料:3K 线碳纤维平织 1ply,母材全部为 PA6
在图11的示例中,碳纤维织物预浸料配置在单面,这对不需要全覆盖的平板或 结构相对容易成型。
5.总结
本文简要回顾了加速汽车轻量化的背景,并概述了CFRP在汽车中的应用流程。通过介绍CFRP应用于汽车的代表性事例,概述了CFRP成型技术在汽车领域的发展动向。在俯瞰创新构造材料的研究和开发整体框架的同时,介绍了其中热塑性CFRP的开发,特别是以名古屋大学复合材料中心项目为焦点进行了重点介绍解说。其核心是LFT-D技术,作为初的成果,明确了需要攻克的课题,并研究出解决方案与措施,在改进成型条件后,可以实现高品质的板状和复杂网格形状的增强结构成型。将来期待进一步完善更高效的设备及底板构造的成型,完成以LFT-D技术为核心的汽车车体下部构造的试制与评估。
1. 汽车轻量化趋势加速的背景
随着环境意识的提高,如图1所示,欧洲、美国和亚洲等正在考虑引入二氧化碳排放法规或燃油效率法规。在严苛的欧洲,2020年已决定将二氧化碳排放量限制在95克/公里以下,并且正在考虑将来引入更严格的限制。美国部分地区有强制供应一定比例以上环保车的举措,在亚洲也在讨论相关措施,预计未来这一举措将进一步加速。如图2所示,每种动力总成的单位距离CO2排放量与车辆重量之间的关系,很明显它们之间存在很强的相关性。从该曲线的斜率来看,车体重量减轻100公斤可以减少20g/km的CO2的排放。也就是说,车辆的轻量化是减少CO2排放的有效方法。
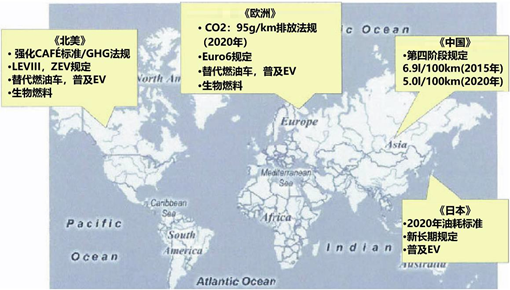
图 1 汽车排放限制及油耗限制动向
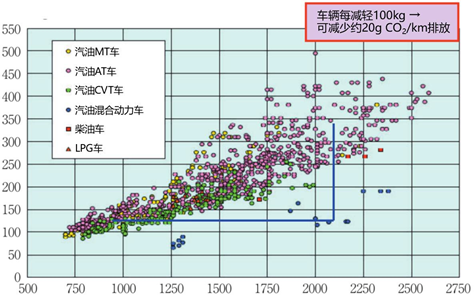
图 2 CO2排放量与车辆重量的关系
2. 汽车的轻量化案例及 CFRP 应用于汽车的基准版车型
在上述背景下,各地的汽车制造商都在开发以轻量化为主要目的的车型。这里着重阐述一下采用CFRP的两个实际应用案例。在量产车中大量使用CFRP的趋势日益增长的今天,德国BMW的电动汽车i3成为大家热议的话题。
如图3所示CFRP的应用说明。为了控制重量,车体使用了约100公斤的CFRP,这在量产乘用车中并不常见。车身的上下壳体是采用环氧树脂的高速RTM工艺成型,用弹性体粘合剂粘合,并将其在铝制底盘通过几个点的结合制造而成。RTM的固化虽然没有达到100℃、5分钟的目标,但实现了非常高速的固化。CFRP的供应链很是复杂的,使用的碳纤维前体是日本厂家提供的,纤维在美国碳化后在德国完成织物,碳纤维碳化所需的电力从便宜的地方调配。虽然它具有电动汽车的特性,但可以说已经确立了一种应用CFRP的理念和方法。
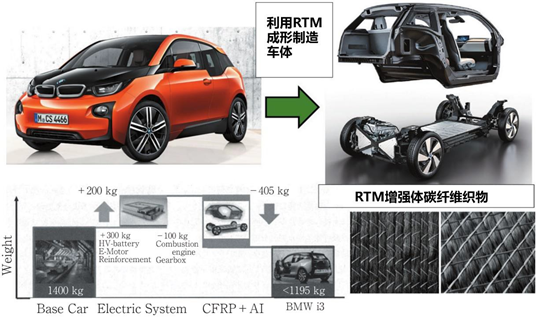
图 3 BMW 推出的电动汽车 i3(CFRP车体)
另一个案例是丰田汽车公司开发的雷克萨斯LFA,作为日本开发的一款实验性跑车,引起了大家的关注。图4展示了驾驶室采用CFRP的各个部件和相对应的技术。似乎有意尝试了各种技术,例如与飞机几乎相同的预浸成型、SMC、以及将树脂压入干织物的RTM等。该车限量生产500辆后停产。
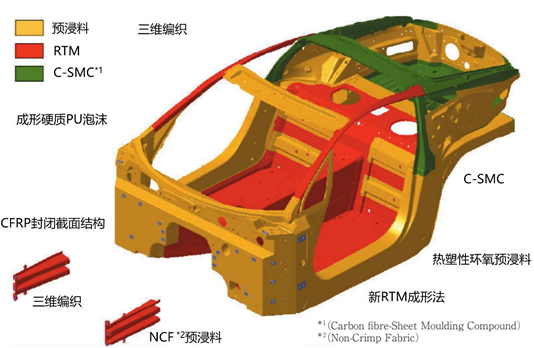
图 4 丰田汽车开发的雷克萨斯 LFA 中使用 CFRP的部品和技术
3.CFRP 成型技术应用于汽车的前景
从目前CFRP在汽车上的应用现状来看,目前CFRP的成本仍然很高,因此除了部分跑车和F1赛车外,其在量产乘用车上的应用还处于起步阶段。不过,主要厂商的研发动力强劲,特别是今后面向量产车的结构部件依次投放市场的动向将加速,其中CFRTP的应用研究在欧洲非常活跃。
作为讨论CFRP在汽车中应用的前提,我们将对CFRP成型技术从飞机到汽车再到通用机械零部件进行全面概述。图5是整个CFRP成型技术的路线图。在飞机的情况下,我们强调以高强度和高刚性为代表的机械性能,并且由于生产零件的数量少,并完成了一项用高压釜这种自动釜对使用连续纤维、热固化树脂的预浸料进行加热固化的技术。因此,作为一种适合稍微提高生产速度的技术,如i3中所述,在完全封闭的阴模中填充碳纤维织物等强化体,注入含有固化剂的树脂,使其尽快固化,即Resin Transfer Molding(RTM)技术。图中左下方向是一种快速成型CFRP的技术,以小齿轮、个人电脑等一般机械零件的情况为例,将含有非常短的碳纤维的热塑性树脂颗粒熔融、注射成型的技术。该图的左下方是一种非常快成型CFRP的技术,以一般机械零件,例如小型齿轮和电脑的壳体为例,将含有非常短的碳纤维的热塑性树脂颗粒熔融、注射成型的技术。由于汽车结构部件的许多部分都需要强度,因此开发了与比注塑成型长的纤维和热塑性树脂混合进行冲压成型的技术。这个代表性例子将在后续章节中叙述。
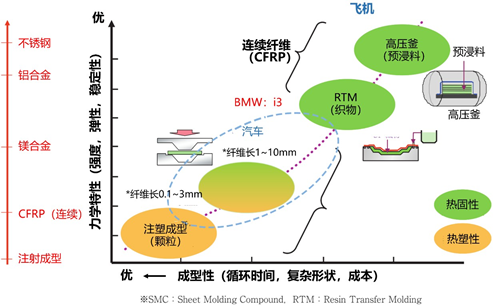
图 5 CFRP 成型技术与力学特性的关系
如图6所示,核心技术LFT-D挤出材料的制造方法概念图。热塑性树脂原料和添加剂的混合物先被熔化并捏合到下一个螺杆轴中,由连续碳纤维束供给的碳纤维束通过与螺杆的碰撞或树脂的剪切场中被切断,并在树脂中剪切力的作用下进行混配。因此很难准确控制纤维的长度,本质上会产生纤维长度的分布。纤维长度的决定因素包括螺杆的转速、纤维·树脂的供给量、搅拌装置内滞留时间、树脂混配时的压力·温度等,这些因素相互之间存在着复杂的影响。碳纤维的长度与所得成型物的力学性能密切相关,除了静态弹性模量和强度之外,冲击特性也很重要,特别是为了维持冲击强度,需要一定长度以上的纤维。
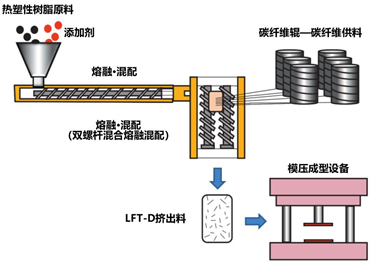
图 6 LFT-D(Long Fiber Thermoplasitic-Direct)的核心—混配体的挤压·制造
未来应用于汽车的 CFRP 成型技术趋势是以 LFT-D 为代表的热塑性树脂/不 连续纤维型 CFRP,以及高压/高速 RTM 与连续碳纤维相结合的 CFRP 应用方向, 预计将根据每种车型的生产速度、零件等扩大应用范围。在热塑性树脂/非连续 纤维型 CFRP 的情况下,假设强度和刚性可能不足,在这种情况下,可以考虑使 用热塑性树脂/连续纤维型 CFRP 增强 LFT-D 的应用。图 7 是 JEC 展会上荷兰Tencate公司出展的采用Tailored LFT-D 工艺生产的汽车零部件的照片。这是 采用德国Fraunhofer 研究机构的 LFT-D 技术,以织物强化热塑 CFRP 为表皮,以 LFT-D 材料为核心的一种夹层材料,弥补了 LFT-D 的强度和刚性不足的问题。这个方法代表将来的一个技术发展方向。
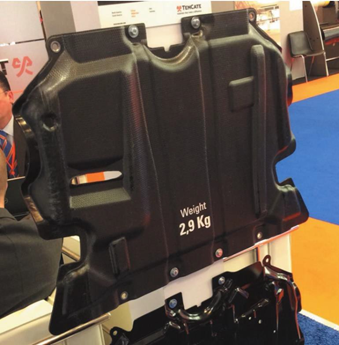
图 7 荷兰 Tencate公司利用 Tailored LFT-D工艺生产的汽车部件
4.名古屋大学复合材料中心(NCC)在汽车用 CFRTP 上的研究
为了应对的发展趋势,名古屋大学NCC在经济产业省直接资助的基础上,从2013年起开始,与东京大学共同启动了致力于用于汽车结构的热塑性CFRTP(Carbon Fiber Reinforced Thermo-Plastic)、结构设计和加工技术的研发。2014年,合作架构发生了一些变化,变成了以NEDO为龙头,经由新设立的“新结构材料技术研究组合(ISMA)”投入项目资金的结构。
在这样的框架下,在名古屋大学NCC开始着手以较少的零件数量、能够降低成本的技术来制造车身(底盘)的研发为目的,在量产车上使用CFRTP。
具体来说,通过引入现有的铝合金制基础车型,设计一个与它几乎相等刚度的车身结构,适当地分割和生产,进行接合、组装构成底盘。作为量产这种底板和侧壁结构的成型技术,考虑采用LFT-D技术。该项目的目标及要点如图8所示。
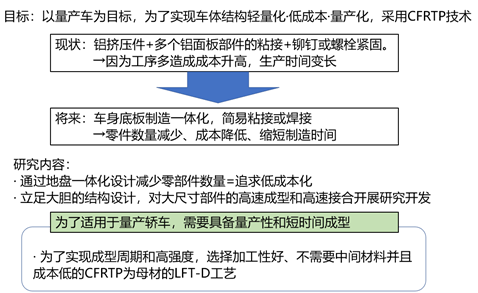
图 8 名古屋大学 NCC 实施的项目目标概要
通过实施该项目,认识到LFT-D成型技术需要克服以下一些关键要素。
(1)由于基体树脂在熔点附近暴露在大气中一段时间是不可避免的,因此需要提 高树脂的抗氧化性。
(2)掌握保持碳纤维长度的技术诀窍与充分使纤维分散之间存在二律背反的关系。
(3)为了保持LFT-D混炼体的良好流动性,需要对其进行适当的温度管理。
(4)确立LFT-D混炼体高速供给和定位的物料搬运技术。
(5)尽可能缩短LFT-D混炼体从挤出到压制成型之间的时间。
为了确保冲击强度,需要保留一定长度的纤维,但如果试图保持纤维长度,则很有可能会受到混炼条件等的限制,在认识到二律背反同时,设定合适的长度目标是技术发展的核心之一。
通过对这些技术课题的认识和改进,当时遇到的一个难题,即高质量平板成形问题通过引入了热风循环炉的保温系统得以顺利解决。此外,通过进行这些技术改进,还可以确保良好的流动性,并且可以在内部形成格子网状的型材(图9)。特别是左图所示,具有高扭转刚度的格子状网的型材,必须利用LFT-D技术才能生产出来,这也预示着该技术发展具有广泛的应用前景。
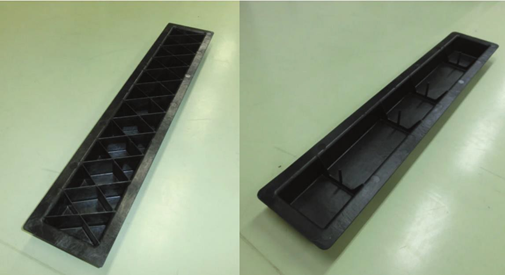
图 9 必须利用 LFT-D 成型技术完成的增强型材
(左:45°格子状 右:90°格子状)
此外,如前文所述,欧洲开发了一种以LFT-D为芯材,热塑性树脂编织预浸料为表面材料的三明治结构。与此同时,NCC成功研制了与图7不同结构的热塑性预浸料的混合成型部件,它使用碳纤维芯材的LFT-D、表面材料采用碳纤维织物作为增强材料。图10、图11展示了在不同形状成型的示例。
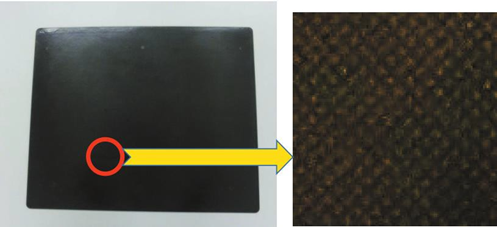
图10 碳纤维织物表面材料/LFT-D 芯材的 CFRTP 混合平板的成形例 表面材料:3K 线碳纤维平织 1ply,母材全部为 PA6
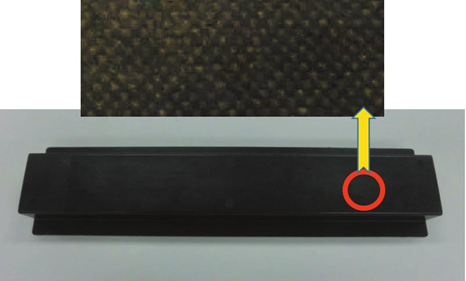
图11 碳纤维织物表面材料/LFT-D 芯材的 CFRTP 帽形的成型例 表面材料:3K 线碳纤维平织 1ply,母材全部为 PA6
在图11的示例中,碳纤维织物预浸料配置在单面,这对不需要全覆盖的平板或 结构相对容易成型。
5.总结
本文简要回顾了加速汽车轻量化的背景,并概述了CFRP在汽车中的应用流程。通过介绍CFRP应用于汽车的代表性事例,概述了CFRP成型技术在汽车领域的发展动向。在俯瞰创新构造材料的研究和开发整体框架的同时,介绍了其中热塑性CFRP的开发,特别是以名古屋大学复合材料中心项目为焦点进行了重点介绍解说。其核心是LFT-D技术,作为初的成果,明确了需要攻克的课题,并研究出解决方案与措施,在改进成型条件后,可以实现高品质的板状和复杂网格形状的增强结构成型。将来期待进一步完善更高效的设备及底板构造的成型,完成以LFT-D技术为核心的汽车车体下部构造的试制与评估。
1. 汽车轻量化趋势加速的背景
随着环境意识的提高,如图1所示,欧洲、美国和亚洲等正在考虑引入二氧化碳排放法规或燃油效率法规。在严苛的欧洲,2020年已决定将二氧化碳排放量限制在95克/公里以下,并且正在考虑将来引入更严格的限制。美国部分地区有强制供应一定比例以上环保车的举措,在亚洲也在讨论相关措施,预计未来这一举措将进一步加速。如图2所示,每种动力总成的单位距离CO2排放量与车辆重量之间的关系,很明显它们之间存在很强的相关性。从该曲线的斜率来看,车体重量减轻100公斤可以减少20g/km的CO2的排放。也就是说,车辆的轻量化是减少CO2排放的有效方法。
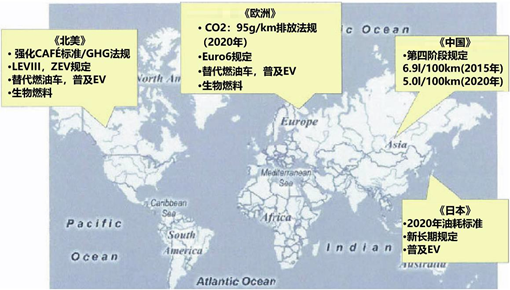
图 1 汽车排放限制及油耗限制动向
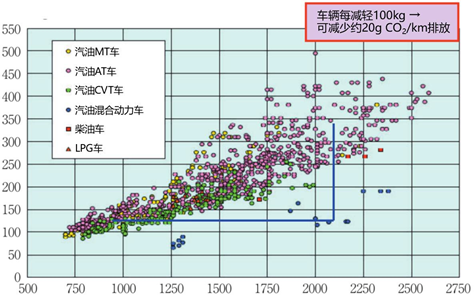
图 2 CO2排放量与车辆重量的关系
2. 汽车的轻量化案例及 CFRP 应用于汽车的基准版车型
在上述背景下,各地的汽车制造商都在开发以轻量化为主要目的的车型。这里着重阐述一下采用CFRP的两个实际应用案例。在量产车中大量使用CFRP的趋势日益增长的今天,德国BMW的电动汽车i3成为大家热议的话题。
如图3所示CFRP的应用说明。为了控制重量,车体使用了约100公斤的CFRP,这在量产乘用车中并不常见。车身的上下壳体是采用环氧树脂的高速RTM工艺成型,用弹性体粘合剂粘合,并将其在铝制底盘通过几个点的结合制造而成。RTM的固化虽然没有达到100℃、5分钟的目标,但实现了非常高速的固化。CFRP的供应链很是复杂的,使用的碳纤维前体是日本厂家提供的,纤维在美国碳化后在德国完成织物,碳纤维碳化所需的电力从便宜的地方调配。虽然它具有电动汽车的特性,但可以说已经确立了一种应用CFRP的理念和方法。
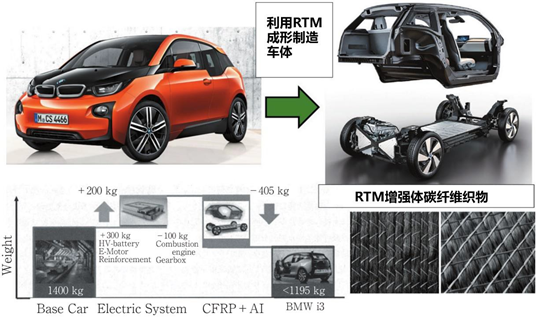
图 3 BMW 推出的电动汽车 i3(CFRP车体)
另一个案例是丰田汽车公司开发的雷克萨斯LFA,作为日本开发的一款实验性跑车,引起了大家的关注。图4展示了驾驶室采用CFRP的各个部件和相对应的技术。似乎有意尝试了各种技术,例如与飞机几乎相同的预浸成型、SMC、以及将树脂压入干织物的RTM等。该车限量生产500辆后停产。
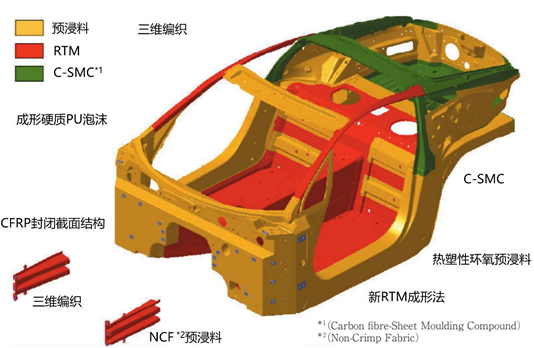
图 4 丰田汽车开发的雷克萨斯 LFA 中使用 CFRP的部品和技术
3.CFRP 成型技术应用于汽车的前景
从目前CFRP在汽车上的应用现状来看,目前CFRP的成本仍然很高,因此除了部分跑车和F1赛车外,其在量产乘用车上的应用还处于起步阶段。不过,主要厂商的研发动力强劲,特别是今后面向量产车的结构部件依次投放市场的动向将加速,其中CFRTP的应用研究在欧洲非常活跃。
作为讨论CFRP在汽车中应用的前提,我们将对CFRP成型技术从飞机到汽车再到通用机械零部件进行全面概述。图5是整个CFRP成型技术的路线图。在飞机的情况下,我们强调以高强度和高刚性为代表的机械性能,并且由于生产零件的数量少,并完成了一项用高压釜这种自动釜对使用连续纤维、热固化树脂的预浸料进行加热固化的技术。因此,作为一种适合稍微提高生产速度的技术,如i3中所述,在完全封闭的阴模中填充碳纤维织物等强化体,注入含有固化剂的树脂,使其尽快固化,即Resin Transfer Molding(RTM)技术。图中左下方向是一种快速成型CFRP的技术,以小齿轮、个人电脑等一般机械零件的情况为例,将含有非常短的碳纤维的热塑性树脂颗粒熔融、注射成型的技术。该图的左下方是一种非常快成型CFRP的技术,以一般机械零件,例如小型齿轮和电脑的壳体为例,将含有非常短的碳纤维的热塑性树脂颗粒熔融、注射成型的技术。由于汽车结构部件的许多部分都需要强度,因此开发了与比注塑成型长的纤维和热塑性树脂混合进行冲压成型的技术。这个代表性例子将在后续章节中叙述。
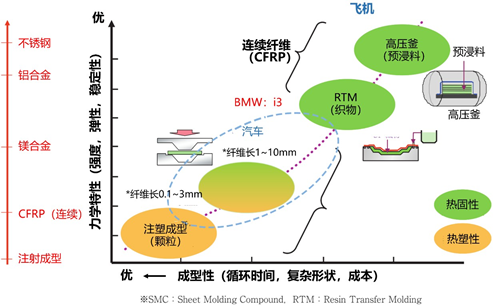
图 5 CFRP 成型技术与力学特性的关系
如图6所示,核心技术LFT-D挤出材料的制造方法概念图。热塑性树脂原料和添加剂的混合物先被熔化并捏合到下一个螺杆轴中,由连续碳纤维束供给的碳纤维束通过与螺杆的碰撞或树脂的剪切场中被切断,并在树脂中剪切力的作用下进行混配。因此很难准确控制纤维的长度,本质上会产生纤维长度的分布。纤维长度的决定因素包括螺杆的转速、纤维·树脂的供给量、搅拌装置内滞留时间、树脂混配时的压力·温度等,这些因素相互之间存在着复杂的影响。碳纤维的长度与所得成型物的力学性能密切相关,除了静态弹性模量和强度之外,冲击特性也很重要,特别是为了维持冲击强度,需要一定长度以上的纤维。
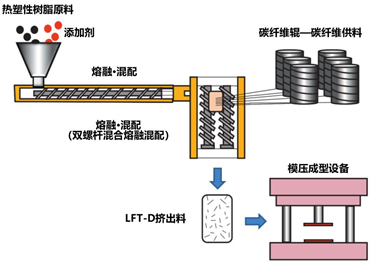
图 6 LFT-D(Long Fiber Thermoplasitic-Direct)的核心—混配体的挤压·制造
未来应用于汽车的 CFRP 成型技术趋势是以 LFT-D 为代表的热塑性树脂/不 连续纤维型 CFRP,以及高压/高速 RTM 与连续碳纤维相结合的 CFRP 应用方向, 预计将根据每种车型的生产速度、零件等扩大应用范围。在热塑性树脂/非连续 纤维型 CFRP 的情况下,假设强度和刚性可能不足,在这种情况下,可以考虑使 用热塑性树脂/连续纤维型 CFRP 增强 LFT-D 的应用。图 7 是 JEC 展会上荷兰Tencate公司出展的采用Tailored LFT-D 工艺生产的汽车零部件的照片。这是 采用德国Fraunhofer 研究机构的 LFT-D 技术,以织物强化热塑 CFRP 为表皮,以 LFT-D 材料为核心的一种夹层材料,弥补了 LFT-D 的强度和刚性不足的问题。这个方法代表将来的一个技术发展方向。
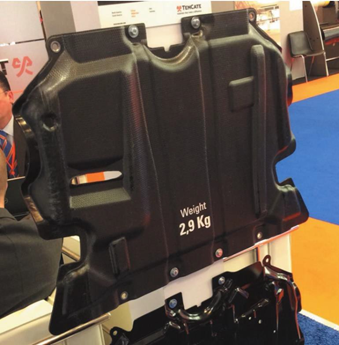
图 7 荷兰 Tencate公司利用 Tailored LFT-D工艺生产的汽车部件
4.名古屋大学复合材料中心(NCC)在汽车用 CFRTP 上的研究
为了应对的发展趋势,名古屋大学NCC在经济产业省直接资助的基础上,从2013年起开始,与东京大学共同启动了致力于用于汽车结构的热塑性CFRTP(Carbon Fiber Reinforced Thermo-Plastic)、结构设计和加工技术的研发。2014年,合作架构发生了一些变化,变成了以NEDO为龙头,经由新设立的“新结构材料技术研究组合(ISMA)”投入项目资金的结构。
在这样的框架下,在名古屋大学NCC开始着手以较少的零件数量、能够降低成本的技术来制造车身(底盘)的研发为目的,在量产车上使用CFRTP。
具体来说,通过引入现有的铝合金制基础车型,设计一个与它几乎相等刚度的车身结构,适当地分割和生产,进行接合、组装构成底盘。作为量产这种底板和侧壁结构的成型技术,考虑采用LFT-D技术。该项目的目标及要点如图8所示。
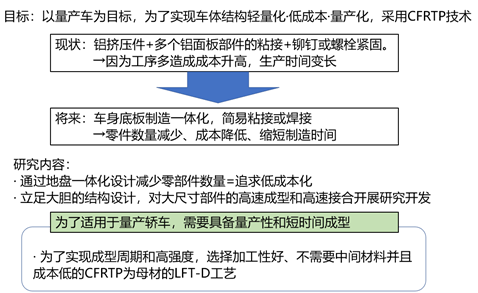
图 8 名古屋大学 NCC 实施的项目目标概要
通过实施该项目,认识到LFT-D成型技术需要克服以下一些关键要素。
(1)由于基体树脂在熔点附近暴露在大气中一段时间是不可避免的,因此需要提 高树脂的抗氧化性。
(2)掌握保持碳纤维长度的技术诀窍与充分使纤维分散之间存在二律背反的关系。
(3)为了保持LFT-D混炼体的良好流动性,需要对其进行适当的温度管理。
(4)确立LFT-D混炼体高速供给和定位的物料搬运技术。
(5)尽可能缩短LFT-D混炼体从挤出到压制成型之间的时间。
为了确保冲击强度,需要保留一定长度的纤维,但如果试图保持纤维长度,则很有可能会受到混炼条件等的限制,在认识到二律背反同时,设定合适的长度目标是技术发展的核心之一。
通过对这些技术课题的认识和改进,当时遇到的一个难题,即高质量平板成形问题通过引入了热风循环炉的保温系统得以顺利解决。此外,通过进行这些技术改进,还可以确保良好的流动性,并且可以在内部形成格子网状的型材(图9)。特别是左图所示,具有高扭转刚度的格子状网的型材,必须利用LFT-D技术才能生产出来,这也预示着该技术发展具有广泛的应用前景。
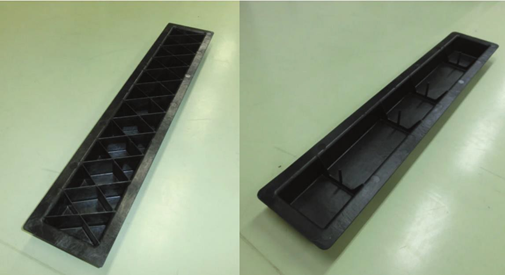
图 9 必须利用 LFT-D 成型技术完成的增强型材
(左:45°格子状 右:90°格子状)
此外,如前文所述,欧洲开发了一种以LFT-D为芯材,热塑性树脂编织预浸料为表面材料的三明治结构。与此同时,NCC成功研制了与图7不同结构的热塑性预浸料的混合成型部件,它使用碳纤维芯材的LFT-D、表面材料采用碳纤维织物作为增强材料。图10、图11展示了在不同形状成型的示例。
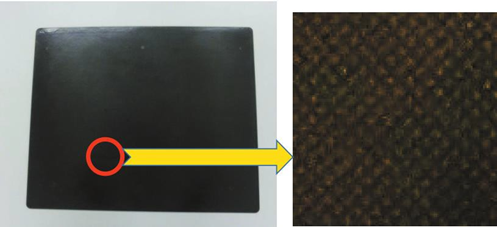
图10 碳纤维织物表面材料/LFT-D 芯材的 CFRTP 混合平板的成形例 表面材料:3K 线碳纤维平织 1ply,母材全部为 PA6
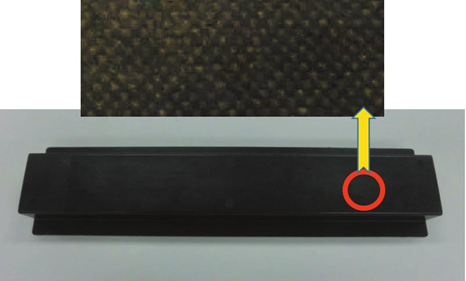
图11 碳纤维织物表面材料/LFT-D 芯材的 CFRTP 帽形的成型例 表面材料:3K 线碳纤维平织 1ply,母材全部为 PA6
在图11的示例中,碳纤维织物预浸料配置在单面,这对不需要全覆盖的平板或 结构相对容易成型。
5.总结
本文简要回顾了加速汽车轻量化的背景,并概述了CFRP在汽车中的应用流程。通过介绍CFRP应用于汽车的代表性事例,概述了CFRP成型技术在汽车领域的发展动向。在俯瞰创新构造材料的研究和开发整体框架的同时,介绍了其中热塑性CFRP的开发,特别是以名古屋大学复合材料中心项目为焦点进行了重点介绍解说。其核心是LFT-D技术,作为初的成果,明确了需要攻克的课题,并研究出解决方案与措施,在改进成型条件后,可以实现高品质的板状和复杂网格形状的增强结构成型。将来期待进一步完善更高效的设备及底板构造的成型,完成以LFT-D技术为核心的汽车车体下部构造的试制与评估。
1. 汽车轻量化趋势加速的背景
随着环境意识的提高,如图1所示,欧洲、美国和亚洲等正在考虑引入二氧化碳排放法规或燃油效率法规。在严苛的欧洲,2020年已决定将二氧化碳排放量限制在95克/公里以下,并且正在考虑将来引入更严格的限制。美国部分地区有强制供应一定比例以上环保车的举措,在亚洲也在讨论相关措施,预计未来这一举措将进一步加速。如图2所示,每种动力总成的单位距离CO2排放量与车辆重量之间的关系,很明显它们之间存在很强的相关性。从该曲线的斜率来看,车体重量减轻100公斤可以减少20g/km的CO2的排放。也就是说,车辆的轻量化是减少CO2排放的有效方法。
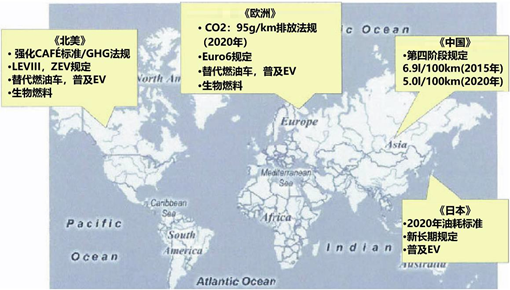
图 1 汽车排放限制及油耗限制动向
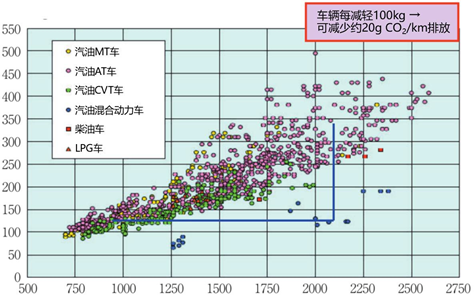
图 2 CO2排放量与车辆重量的关系
2. 汽车的轻量化案例及 CFRP 应用于汽车的基准版车型
在上述背景下,各地的汽车制造商都在开发以轻量化为主要目的的车型。这里着重阐述一下采用CFRP的两个实际应用案例。在量产车中大量使用CFRP的趋势日益增长的今天,德国BMW的电动汽车i3成为大家热议的话题。
如图3所示CFRP的应用说明。为了控制重量,车体使用了约100公斤的CFRP,这在量产乘用车中并不常见。车身的上下壳体是采用环氧树脂的高速RTM工艺成型,用弹性体粘合剂粘合,并将其在铝制底盘通过几个点的结合制造而成。RTM的固化虽然没有达到100℃、5分钟的目标,但实现了非常高速的固化。CFRP的供应链很是复杂的,使用的碳纤维前体是日本厂家提供的,纤维在美国碳化后在德国完成织物,碳纤维碳化所需的电力从便宜的地方调配。虽然它具有电动汽车的特性,但可以说已经确立了一种应用CFRP的理念和方法。
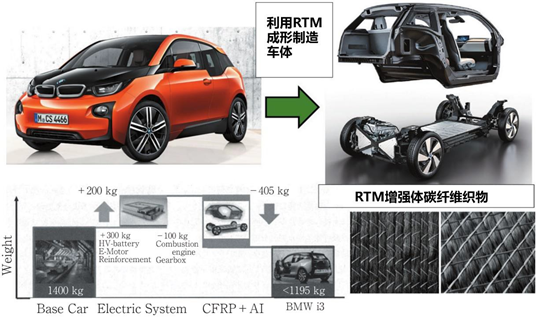
图 3 BMW 推出的电动汽车 i3(CFRP车体)
另一个案例是丰田汽车公司开发的雷克萨斯LFA,作为日本开发的一款实验性跑车,引起了大家的关注。图4展示了驾驶室采用CFRP的各个部件和相对应的技术。似乎有意尝试了各种技术,例如与飞机几乎相同的预浸成型、SMC、以及将树脂压入干织物的RTM等。该车限量生产500辆后停产。
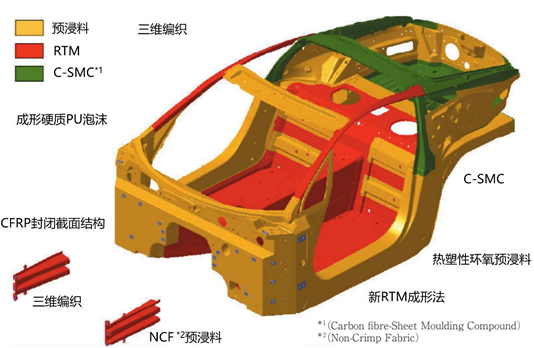
图 4 丰田汽车开发的雷克萨斯 LFA 中使用 CFRP的部品和技术
3.CFRP 成型技术应用于汽车的前景
从目前CFRP在汽车上的应用现状来看,目前CFRP的成本仍然很高,因此除了部分跑车和F1赛车外,其在量产乘用车上的应用还处于起步阶段。不过,主要厂商的研发动力强劲,特别是今后面向量产车的结构部件依次投放市场的动向将加速,其中CFRTP的应用研究在欧洲非常活跃。
作为讨论CFRP在汽车中应用的前提,我们将对CFRP成型技术从飞机到汽车再到通用机械零部件进行全面概述。图5是整个CFRP成型技术的路线图。在飞机的情况下,我们强调以高强度和高刚性为代表的机械性能,并且由于生产零件的数量少,并完成了一项用高压釜这种自动釜对使用连续纤维、热固化树脂的预浸料进行加热固化的技术。因此,作为一种适合稍微提高生产速度的技术,如i3中所述,在完全封闭的阴模中填充碳纤维织物等强化体,注入含有固化剂的树脂,使其尽快固化,即Resin Transfer Molding(RTM)技术。图中左下方向是一种快速成型CFRP的技术,以小齿轮、个人电脑等一般机械零件的情况为例,将含有非常短的碳纤维的热塑性树脂颗粒熔融、注射成型的技术。该图的左下方是一种非常快成型CFRP的技术,以一般机械零件,例如小型齿轮和电脑的壳体为例,将含有非常短的碳纤维的热塑性树脂颗粒熔融、注射成型的技术。由于汽车结构部件的许多部分都需要强度,因此开发了与比注塑成型长的纤维和热塑性树脂混合进行冲压成型的技术。这个代表性例子将在后续章节中叙述。
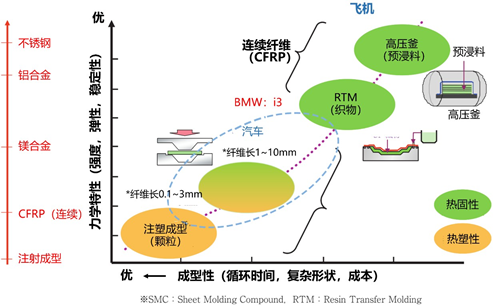
图 5 CFRP 成型技术与力学特性的关系
如图6所示,核心技术LFT-D挤出材料的制造方法概念图。热塑性树脂原料和添加剂的混合物先被熔化并捏合到下一个螺杆轴中,由连续碳纤维束供给的碳纤维束通过与螺杆的碰撞或树脂的剪切场中被切断,并在树脂中剪切力的作用下进行混配。因此很难准确控制纤维的长度,本质上会产生纤维长度的分布。纤维长度的决定因素包括螺杆的转速、纤维·树脂的供给量、搅拌装置内滞留时间、树脂混配时的压力·温度等,这些因素相互之间存在着复杂的影响。碳纤维的长度与所得成型物的力学性能密切相关,除了静态弹性模量和强度之外,冲击特性也很重要,特别是为了维持冲击强度,需要一定长度以上的纤维。
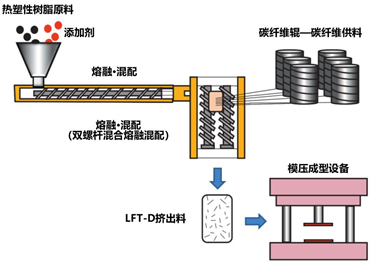
图 6 LFT-D(Long Fiber Thermoplasitic-Direct)的核心—混配体的挤压·制造
未来应用于汽车的 CFRP 成型技术趋势是以 LFT-D 为代表的热塑性树脂/不 连续纤维型 CFRP,以及高压/高速 RTM 与连续碳纤维相结合的 CFRP 应用方向, 预计将根据每种车型的生产速度、零件等扩大应用范围。在热塑性树脂/非连续 纤维型 CFRP 的情况下,假设强度和刚性可能不足,在这种情况下,可以考虑使 用热塑性树脂/连续纤维型 CFRP 增强 LFT-D 的应用。图 7 是 JEC 展会上荷兰Tencate公司出展的采用Tailored LFT-D 工艺生产的汽车零部件的照片。这是 采用德国Fraunhofer 研究机构的 LFT-D 技术,以织物强化热塑 CFRP 为表皮,以 LFT-D 材料为核心的一种夹层材料,弥补了 LFT-D 的强度和刚性不足的问题。这个方法代表将来的一个技术发展方向。
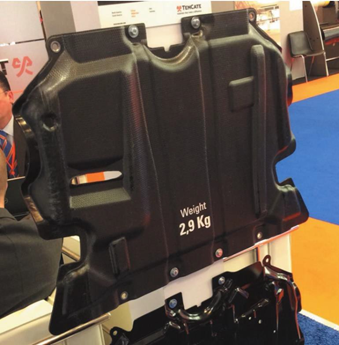
图 7 荷兰 Tencate公司利用 Tailored LFT-D工艺生产的汽车部件
4.名古屋大学复合材料中心(NCC)在汽车用 CFRTP 上的研究
为了应对的发展趋势,名古屋大学NCC在经济产业省直接资助的基础上,从2013年起开始,与东京大学共同启动了致力于用于汽车结构的热塑性CFRTP(Carbon Fiber Reinforced Thermo-Plastic)、结构设计和加工技术的研发。2014年,合作架构发生了一些变化,变成了以NEDO为龙头,经由新设立的“新结构材料技术研究组合(ISMA)”投入项目资金的结构。
在这样的框架下,在名古屋大学NCC开始着手以较少的零件数量、能够降低成本的技术来制造车身(底盘)的研发为目的,在量产车上使用CFRTP。
具体来说,通过引入现有的铝合金制基础车型,设计一个与它几乎相等刚度的车身结构,适当地分割和生产,进行接合、组装构成底盘。作为量产这种底板和侧壁结构的成型技术,考虑采用LFT-D技术。该项目的目标及要点如图8所示。
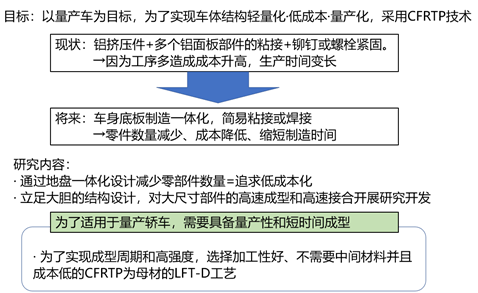
图 8 名古屋大学 NCC 实施的项目目标概要
通过实施该项目,认识到LFT-D成型技术需要克服以下一些关键要素。
(1)由于基体树脂在熔点附近暴露在大气中一段时间是不可避免的,因此需要提 高树脂的抗氧化性。
(2)掌握保持碳纤维长度的技术诀窍与充分使纤维分散之间存在二律背反的关系。
(3)为了保持LFT-D混炼体的良好流动性,需要对其进行适当的温度管理。
(4)确立LFT-D混炼体高速供给和定位的物料搬运技术。
(5)尽可能缩短LFT-D混炼体从挤出到压制成型之间的时间。
为了确保冲击强度,需要保留一定长度的纤维,但如果试图保持纤维长度,则很有可能会受到混炼条件等的限制,在认识到二律背反同时,设定合适的长度目标是技术发展的核心之一。
通过对这些技术课题的认识和改进,当时遇到的一个难题,即高质量平板成形问题通过引入了热风循环炉的保温系统得以顺利解决。此外,通过进行这些技术改进,还可以确保良好的流动性,并且可以在内部形成格子网状的型材(图9)。特别是左图所示,具有高扭转刚度的格子状网的型材,必须利用LFT-D技术才能生产出来,这也预示着该技术发展具有广泛的应用前景。
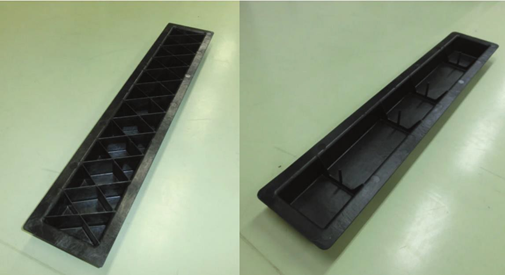
图 9 必须利用 LFT-D 成型技术完成的增强型材
(左:45°格子状 右:90°格子状)
此外,如前文所述,欧洲开发了一种以LFT-D为芯材,热塑性树脂编织预浸料为表面材料的三明治结构。与此同时,NCC成功研制了与图7不同结构的热塑性预浸料的混合成型部件,它使用碳纤维芯材的LFT-D、表面材料采用碳纤维织物作为增强材料。图10、图11展示了在不同形状成型的示例。
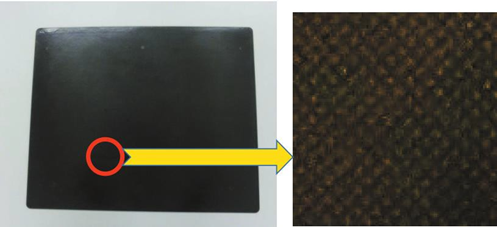
图10 碳纤维织物表面材料/LFT-D 芯材的 CFRTP 混合平板的成形例 表面材料:3K 线碳纤维平织 1ply,母材全部为 PA6
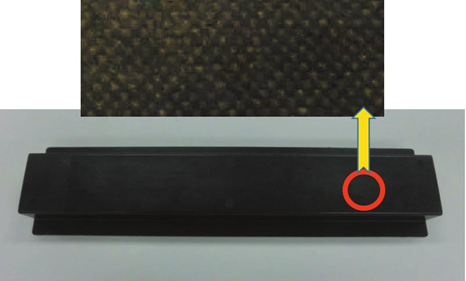
图11 碳纤维织物表面材料/LFT-D 芯材的 CFRTP 帽形的成型例 表面材料:3K 线碳纤维平织 1ply,母材全部为 PA6
在图11的示例中,碳纤维织物预浸料配置在单面,这对不需要全覆盖的平板或 结构相对容易成型。
5.总结
本文简要回顾了加速汽车轻量化的背景,并概述了CFRP在汽车中的应用流程。通过介绍CFRP应用于汽车的代表性事例,概述了CFRP成型技术在汽车领域的发展动向。在俯瞰创新构造材料的研究和开发整体框架的同时,介绍了其中热塑性CFRP的开发,特别是以名古屋大学复合材料中心项目为焦点进行了重点介绍解说。其核心是LFT-D技术,作为初的成果,明确了需要攻克的课题,并研究出解决方案与措施,在改进成型条件后,可以实现高品质的板状和复杂网格形状的增强结构成型。将来期待进一步完善更高效的设备及底板构造的成型,完成以LFT-D技术为核心的汽车车体下部构造的试制与评估。