轻量化材料技术交流
碳纤维复合材料(CFRP)主导
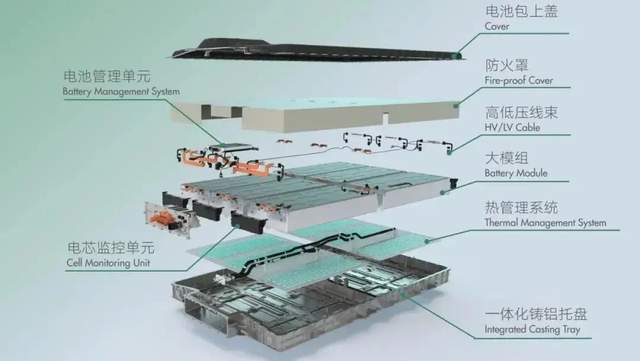
特斯拉Model S/X采用碳纤维复合材料(CFRP)车身部件实现减重30%且刚度提升50%,高端车型已将其作为标配。
电池包应用CFRP替代铝壳可减重40%,如上汽开发的树脂基碳纤维框架使整包质量减少16%,同时提升耐腐蚀性和热管理效能。
金属与复合材料混合应用
宁德时代玄武岩纤维强化铝合金电池壳实现26%体积优化;比亚迪采用SMC复合材料上盖+高强铝下壳体组合方案。
泡沫铝夹层结构(如0.5mm碳纤维+3mm泡沫铝)提升弯曲刚度30%,满足IP67防水与阻燃要求。
纳米改性技术进展
添加1wt%二氧化硅纳米粒子使树脂粘度降低18%,玻璃化转变温度提高15℃6;石墨烯薄膜层提升能量密度4%。
结构设计创新
力学集成优化
广汽三维网状铝基支架提升模组间载荷分布效率45%;宁德时代CTP5.0平台使单体载荷自持率从78%升至92%。
拓扑优化设计(如SMC上盖板)将共振频率降至120Hz以下,减少振动疲劳损伤3。
热管理架构重构
比亚迪蒸汽直触散热管道取代液冷机构,辅助系统减重13.7%且温度均一性标准差<0.9℃。
吉利环形石墨烯相变模组提升自然循环散热占比至56%。
制造工艺与成本控制
高效成型技术
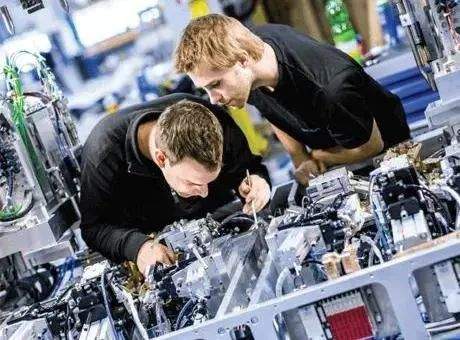
RTM工艺缩短固化周期至2小时内,适合大规模生产;热塑性复合材料(如PA6+GF)采用D-LFT工艺,单件生产时间≤3分钟,效率提升80%。
3D打印实现连续纤维增强65%体积含量,加速电池托盘原型开发。
回收与成本挑战
热塑性复材回收率达90%,但热压罐成型设备成本占比仍高达60%;碳纤维原材料成本制约其经济型车型应用。
技术瓶颈与未来方向
核心难题
复合材料多场耦合行为参数失配,极值工况下功能属性衰退率超80%;
电磁仿真与力学构态存在20%-30%参数偏差;界面应力疲劳引发安全风险(如合资品牌召回事件)。
战略突破点
金属锂复合正极+纳米合金异形支架体系级减重14%;
无粘结剂微穿孔成型技术能耗指数降至1.45临界值;
碳化硅负极预锂化工艺削减金属基板支撑面积38%。
产业应用趋势
高端市场:碳纤维复合材料(CFRP)主导(特斯拉、宁德时代);
中端车型:铝玻混杂复材(广汽AION S底盘);
经济车型:钢制箱体仍为主流5,SMC复材渗透率提升。
注:大众-宁德联合实验室复合自补偿支撑结构碰撞导引效率达67%,已突破量产基准。