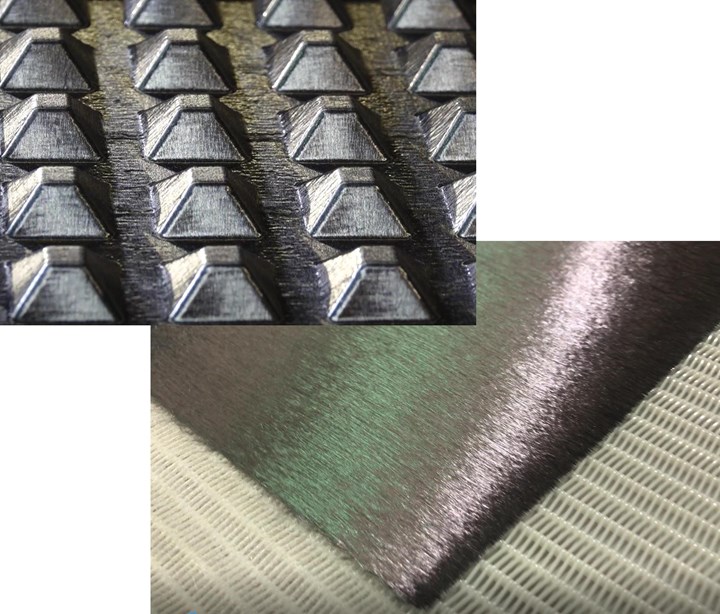
用于经济实惠复杂形状复合材料零件的TuFF短纤维片材
UD-CCM开发可定制的板材通用成型原料(TuFF),由于高度的纤维排列和长度控制,可达到UD预浸料级的纤维体积和性能(此处显示的是IM7纤维),易于成型,由于其在平面内可拉伸所以形状复杂。所有图像的来源| 特拉华大学CCM
美国国防高级研究计划局(DARPA)于2015年启动“量身定制的原料和形状(TFF)”计划,以实现快速、低成本和敏捷地制造重量小于20磅的复杂几何形状复合材料零件。复合材料代替金属,而这些金属可通过自动胶带铺放和纤维铺放(ATL / AFP)等工艺制成大型而坚固的表皮。但是,典型的战术军事机体中80%以上的零件很小,而且几何形状复杂。因此,机加工铝由于复合材料的高成本和复杂性以及小零件的制造而受到青睐。
“您可以购买4至6英寸的铝板,将其放入CNC加工中心并按一下按钮,”复合材料行业和TFF计划顾问Jeff Hendrix说。 “尽管金属零件制造成本较低,但它们的额外重量以及对裂纹和腐蚀的敏感性导致该系统的性能欠佳。” DARPA国防科学办公室项目经理Mick Maher解释说。(尽管Maher于2016年完成DARPA的五年任期,但他对TFF的愿景已由现任DARPA计划经理Jan Vandenbrande博士分享。)Hendrix指出,“没有人会为复合材料在小部件上提供的重量节省支付双倍的费用;复合材料必须在成本上比铝更有竞争力。”
为了实现这一目标,TFF分为两个子程序-个子程序在第1部分中讨论材料(原料),第二个子程序在下个月的第2部分中探讨成型(成型):
1.由美国特拉华大学(UD)复合材料中心(UD-CCM)领导的可定制通用成型原料(TuFF)
2.由波音公司领导的快速高性能制造(RAPM,发音为“ wrap-em”)。
1.由美国特拉华大学(UD)复合材料中心(UD-CCM)领导的可定制通用成型原料(TuFF)
2.由波音公司领导的快速高性能制造(RAPM,发音为“ wrap-em”)。
TuFF原料是高度对准的不连续纤维预成型件,呈薄层状,可与热塑性(TP)或热固性(TS)树脂混合用于预浸料,或以干燥形式用于基于灌注的工艺。已在UD-CCM的5吨/年试验设施中证明正在申请的不连续纤维对准和预成型工艺,该工艺包括:
短纤维分散和校准
自动上料和堆叠
预浸料和量身定制的坯料生产
TS/TP成型和液体成型单元,将于2020年第三季度增加。
校准过程与纤维无关,TuFF预成型坯已用航空航天级聚丙烯腈(PAN)碳纤维(例如IM7、T800)、沥青碳纤维、再生碳纤维、玻璃和陶瓷纤维制造。在成形过程中,具有小于1%的空隙和高达63%的纤维体积的层压板在成型过程中已显示出> 40%的双轴面内应变能力,可实现复杂几何形状的金属样成型而没有产生飞溅或复杂的层板模式。试生产线还展示TuFF工艺废料中纤维的闭环回收和再利用,旨在实现零废料生产。TuFF在美国复合材料制造商协会(ACMA)举办的CAMX 2019上获得“无限可能市场增长奖”。
开发不连续的纤维原料
连续碳纤维对TFF应用存在两个问题:价格昂贵且难以形成复杂的形状。 短纤维具有可成形性,但是目前的形式和工艺(例如注塑)不能提供所需的高纤维体积特性(图1)。 另一个问题是,如何在越来越分散的国防部市场上以低的业务量,针对特定任务的平台上摊销高昂的工具和零件开发成本。
UD-CCM和TuFF主要研究人员的主管John W. Gillespie,Jr.博士补充说:“复合材料零件因独特的零件/过程/程序认证而价格昂贵”。 因此,TuFF的目标是开发一种具有类似于金属的可成型性材料,也可以进行定制以满足多种DoD应用需求和体积。
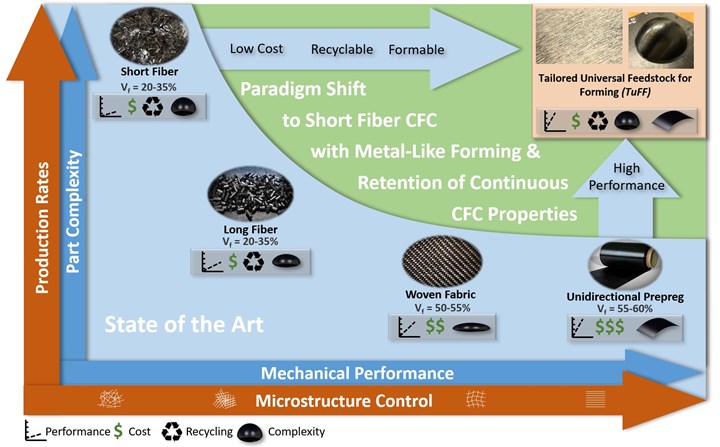
图1:短纤维规格,长纤维性能,可成型以降低零件成本
DARPA资助的TuFF是一种通用材料,可以针对特定的零件和程序要求进行定制,能使复合材料在国防应用中与小型零件(<10公斤)的机加工铝材抗衡,因为铝已占据主要市场,即使是商用飞机和汽车的新技术对复合材料的使用也很小。
Yarlagadda说:“ TuFF项目旨在应对关键挑战,包括如何制造直径更小的短碳纤维,以使复合材料具有航空航天性能。”“我们的想法是采用低成本的沥青前驱体,直接制成短纤维,目的是提高中间模量碳纤维的性能。” 该项目包括德雷克塞尔大学,弗吉尼亚理工学院暨州立大学和克莱姆森大学作为分包商,后者负责大部分分包商的工作。
Yarlagadda解释说:“这是一个具有挑战性的问题,因为您看到的是与用于生产连续纤维的工艺截然不同的工艺。” Clemson沥青纤维的多次迭代已经通过多次评估,但要开发和成熟沥青纤维技术仍需要DARPA TuFF项目以外的其他工作。 因此,这里给出的TuFF结果是使用商业的、连续的短切PAN纤维来实现的。成本影响将在下面讨论。
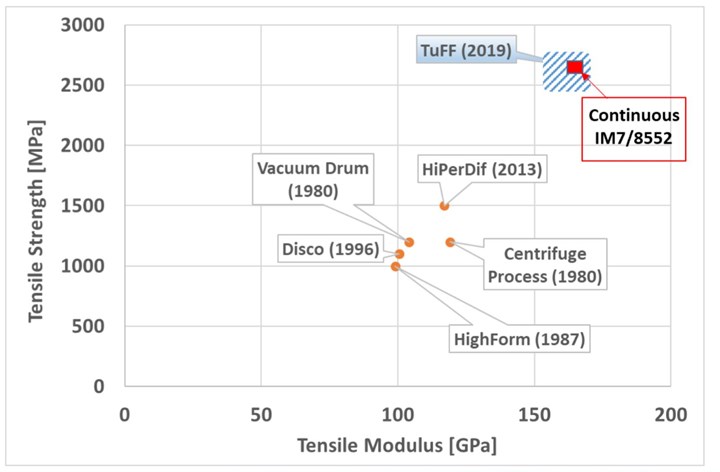
图2:短纤维材料的历史
TuFF能够严格控制纤维长度,以可成形性的佳点之内的长宽比进行对齐。
数十年来,人们一直在寻求便宜,可成型复合材料的短碳纤维解决方案(图2),包括DiscoTex,拉伸断裂碳纤维(SBCF)和HiPerDif(高性能不连续纤维)。 对于SBCF,机械过程将连续的PAN碳纤维断裂成25至50毫米或更长的长度。 使用的直径为0.005毫米的赫氏公司IM7碳纤,其长宽比为10,000。 Yarlagadda解释说:“长宽比大于10,000需要高成型力,”他指出可成型性的佳点是长宽比在100到1,000之间。TuFF使用3毫米长的IM7光纤,纵横比为600。“从1990年代后期发表的技术论文可以看出,长径比为100的短纤维应与连续纤维的刚度相匹配,长径比为1,000的短纤维也应与强度相匹配,但是光纤对准存在问题。”” Yarlagadda说。
HiPerDiF是由英国布里斯托尔大学(Bristol University)开发的能够使用一系列不同长度(长度从1毫米到12毫米不等)的碳纤维原料,这些原料悬浮在水中并从喷嘴沉积到基板上,从而形成一种排列整齐的纤维预制体。因此,与SBCF相比,HiPerDiF改善光纤排列,但报告67%的光纤在单向±3度以内。 TuFF可实现> 95%的纤维在所需方向的5度范围内排列。
受控,均匀的微观结构
UD-CCM的助理总监兼TuFF项目负责人Dirk Heider解释说:“通过高水平的光纤对准,我们得到与单向预浸料相同的光纤量。” 他指出,已证明使用3毫米长的IM7碳纤维将复合材料的纤维体积控制在40%至63%之间。
另一个关键因素是光纤长度控制。95%的IM7光纤长2.8至3.2毫米(标称值为3±0.2毫米)。 “具有完全一致的纤维长度,可以优化机械性能和成型性能,以实现可重复的利用。” Gillespie解释说。Heider补充说,IM7纤维长度为3毫米足以在降低成型压力和模具成本的同时提供完整的性能转换。 他观察到:“无论纤维类型如何,我们都能控制微观结构。” Yarlagadda补充说:“如果您具有一致的微观结构,那么您将具有整体一致的响应,从而在成型过程中产生一致的零件厚度。”
两个尺寸不是一个因素。海德说。 “必须在细丝水平上对齐获得这种特性和受控的微观结构的转换。 我们将从外部供应商处收到切碎的IM7丝束分散在水中以细丝化。 以非常可控的方式将细丝以高度对齐的形式沉积为片状,再纤维放回。” 正在申请的TuFF工艺可生产单层(8微米厚)的纤维片,将其堆叠成定制的铺层,切成空白或切成胶带。 薄层指的是散布的丝束-例如,通常将5毫米宽的12K高强度(HS)碳纤维丝束散布到25毫米宽的胶带上。 Heider指出,“ 我们演示了一种极具操控性的薄层胶带,半径达到1英寸,而连续纤维胶带则为40-50英寸。”
Heider说,使用标准模量光纤的直径大约为7微米(0.007毫米),这意味着TuFF所需的长宽比为100-1,000时,光纤长度为4至5毫米。 他还指出,复合材料的性能不仅取决于纤维,还取决于树脂和树脂与纤维的界面。 Heider说:“我们一直在使用经过商业处理的纤维,该纤维经过表面处理,没有上浆,可用于航空航天热塑性和环氧基体树脂。 “我们在SAMPE 2019上发表的论文中都有报道。TuFF在短纤维和树脂之间显示出良好的粘合性。”
航空航天性能,类似金属的可成型性
“我们正在用PEI(聚醚酰亚胺)和PEKK(聚醚酮酮)热塑性塑料和Hexcel 8552环氧树脂(用于HexPly单向预浸料中)测试对齐的短纤维材料,以证明航空级复合材料的性能,”Gillespie说。 PEI的测试已经完成,其显示的复合材料性能与整个板上的连续碳纤维相同(图3),包括拉伸,压缩和剪切以及开孔拉伸和压缩(OHT / OHC)等缺口性能 和轴承强度。 目前正在进行PEKK和8552环氧树脂的测试,并将于今年完成。
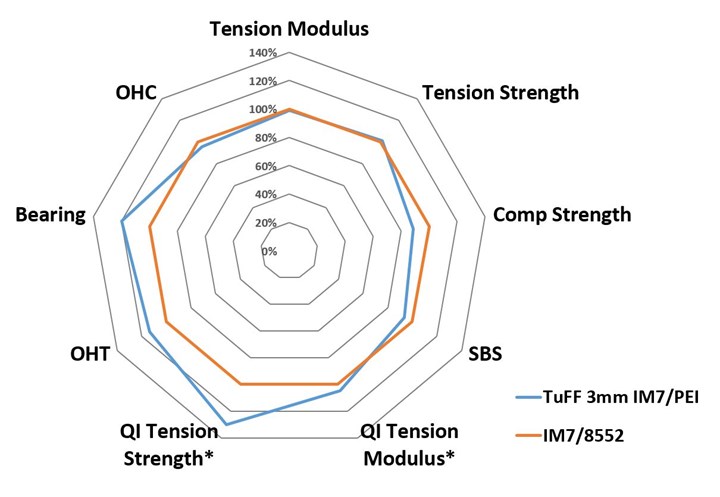
图3:获得UD预浸料的性能
在初步测试中,与标准的IM7 / 8552环氧预浸料相比,在初步测试中,薄层(60 gsm60-微米厚)IM7PEI材料的某些性能甚至比标准IM78552环氧prepreg有所提高(见下文),这要归功于薄层的微观结构。
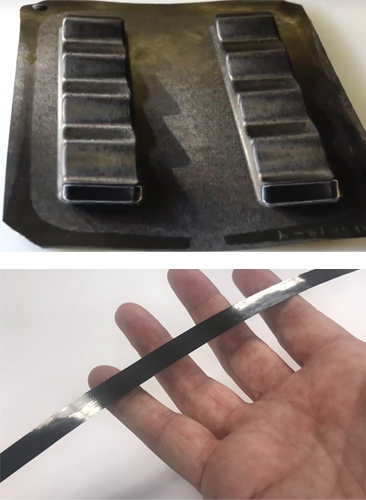
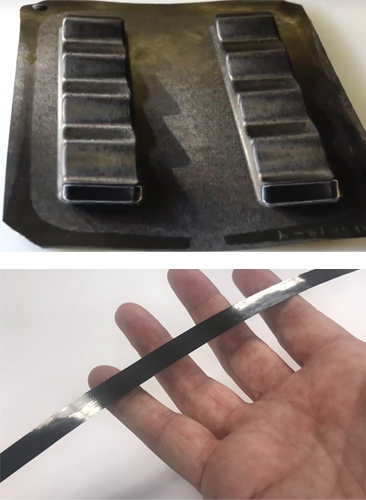
图4:复杂形状的薄带
TuFF的短纤维和均匀的微观结构可以形成航空质量的复杂形状,复杂的形状没有高压或复杂的温度控制。该材料也可以被分割成连续的磁带用于AFP处理。
Yarlagadda说:“我们能够生产出少于1%空隙的复合层压板。” “我们还展示了与UD热固性预浸料和热塑性预浸料相当的性能,以及薄TuFF格式的一些初步数据。” 薄层增强材料已被证明可以提高承载能力并减少裂纹扩展,从而具有更高的损伤承受能力(请参阅了解更多信息)。 Yarlagadda补充说:“初步数据表明,由于薄的微观结构,其抗拉强度提高了30%。”
他补充说:“该材料在平面内可拉伸,因此可以像金属一样成型。” TuFF已形成具有大于40%的双轴应变的零件几何形状。 “我们像金属成型工艺一样,保留并塑造边界。” 已经证明TuFF的可成型性适用于一系列叠层,包括0度和90度单向(UD),0/90双轴和准各向同性。 图4和下面的视频中的图像(请参阅了解更多信息)还展示了一系列复杂形状的零件。 “我们从薄型零件开始,因为无法隐藏缺陷。”
图5 –光纤到零件中试验
UD-CCM已经安装了一个5吨的试验工厂,该工厂生产连续的TuFF片材和预浸料以及量身定制的坯料,这些料将用于其柔性制造单元中,用于加工形状大为0.9 x 1.2米(3 x 4英尺)的复杂形状零件 。
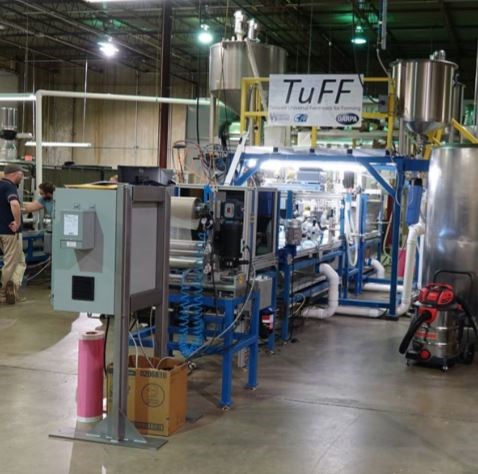
校准
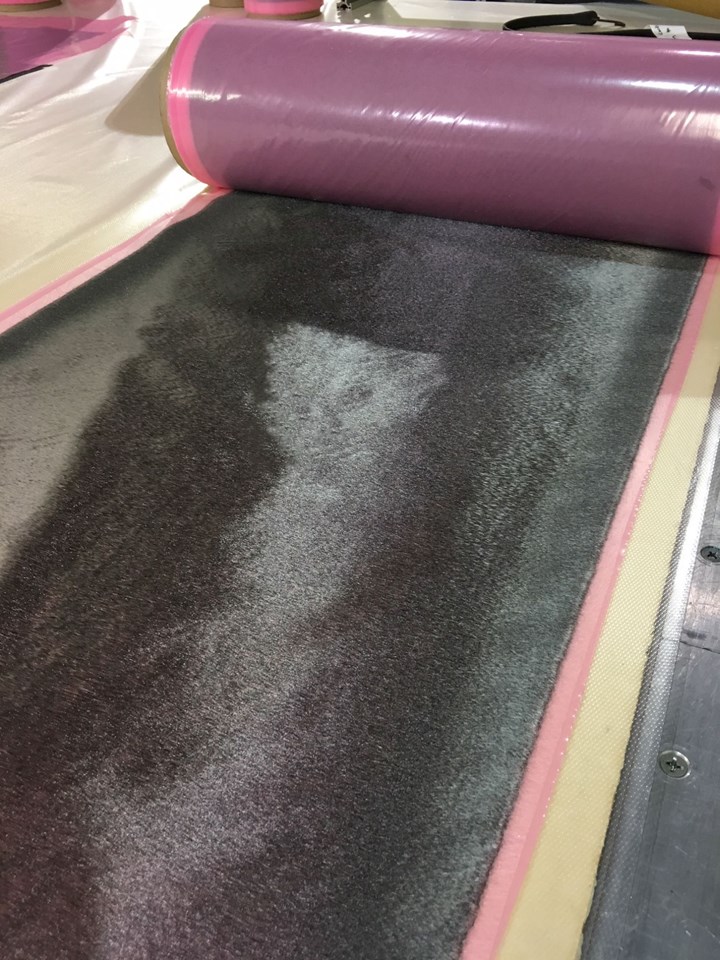
单TuFF薄板(8 gsm)
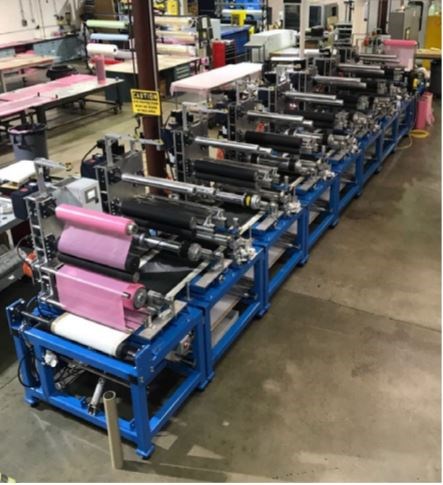
堆放
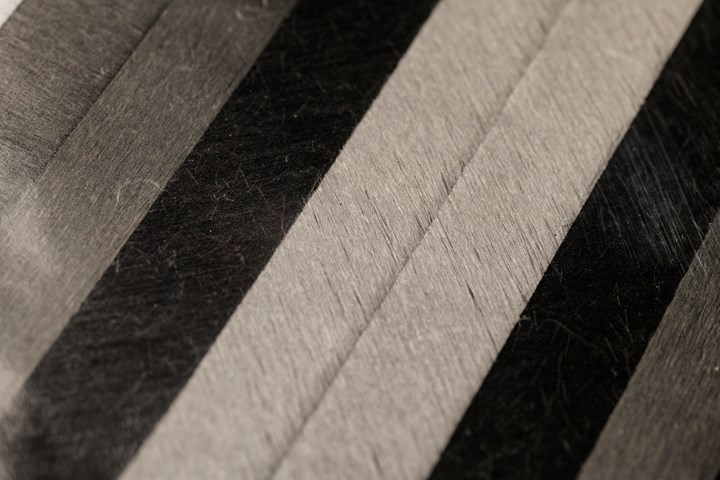
4-8 TuFF层(30-60 gsm)
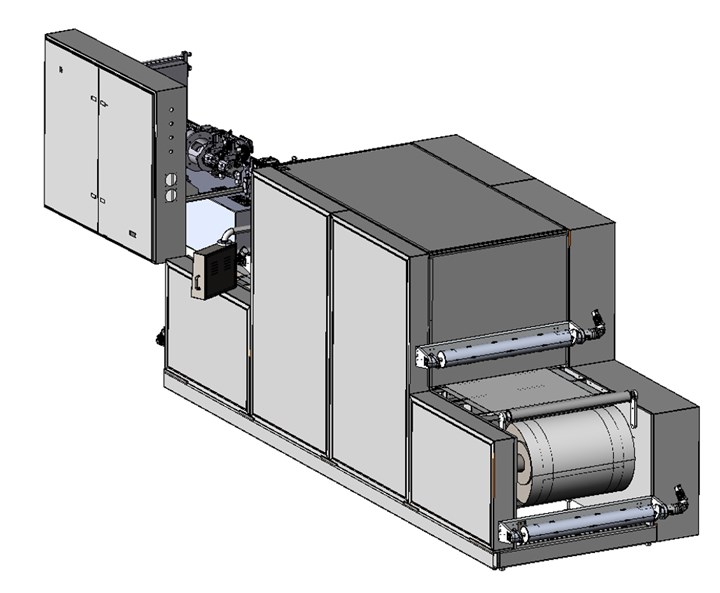
预浸
薄膜浸渍(8层TuFF:1层PEI)
(PEI膜厚25微米)
相当于TS预浸料:24 TuFF层(195 gsm)
相当于TP预浸料:16 TuFF层(130 gsm)
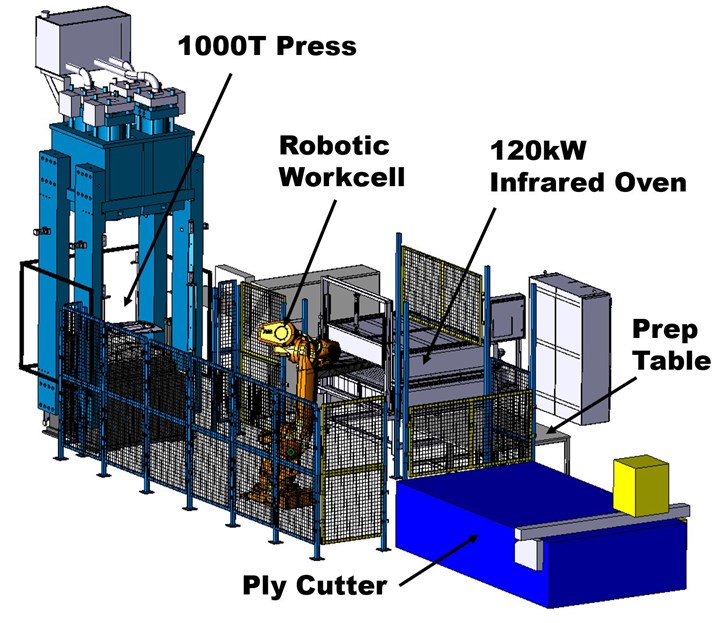
形成元件
机器人工作单元
120千瓦红外线烤箱
1000吨压力机
HP-RTM或湿压成型
光纤到零件中试工厂
UD-CCM的高级科学家,TuFF的共同发明者John Tierney博士说:“在DARPA计划中,我们的目标之一就是超越实验室规模的系统。” “经过几次迭代,我们目前有两条24英寸宽的线用于制造对齐的短纤维片材:一条标准线和一条偏轴线,用于产生倾斜的纤维取向(例如45、30、60度)。 ”这些生产线的标准薄板是连续的薄层材料,厚8微米,大约8克/平方米(图5)。纸卷被卷绕到卷筒上,然后卷筒被装载到邻近的自动堆垛系统中在内部建造,这需要单独的卷并堆叠多达八层,以构建所需的纤维面积重量和纤维取向叠层,从而产生30-190克/平方米和30-190微米厚的标准预浸料和坯料。Yarlagadda指出:“用于预浸料坯和量身定制的第三台机器大多是现成的,但可以定制以处理我们的材料。” “在这台机器之前,我们一直在使用树脂膜工艺,用树脂膜将堆叠的薄片分层,然后施加热量和压力进行固结。半连续分度压力机设计使我们能够制造预浸料或定制的热塑性坯料。”
他解释说,制造坯料的过程不是将胶带粘贴到旋转台上的AFP过程。 “它遵循标准的复合铺层方法,其中定制的坯料设计决定了铺层顺序。 TuFF可以做的是简化毛坯几何形状,消除复杂的带和铺层形状,因为平面内拉伸功能允许进行复杂的成型。” Heider解释说,在随后的成形单元中,该单元可以生产高达0.9 x 1.2米的零件。 我们还创造了干燥的坯料,并将其模制成液体树脂灌注的形状。” 这项工作是由UD-CCM’s small-company incubator的Composites Automation LLC完成的,公司也位于纽瓦克市。 “结果看起来很有希望,” Heider补充说。 “我们可以使用热塑性面纱来稳定材料,然后轻松地对其进行预成型,然后进行灌注。”
Tierney强调说,这个具有集成自动化功能且年产能为5吨/年的试验工厂证明了TuFF技术的工业可扩展性。 他解释说:“所有硬件都反映了一个完整工厂的样子。” “它目前正在提供我们的材料特性测试和成型演示所需的材料。”
成本,光纤到零件的转换,零浪费
TuFF已显示出以高成形性满足航空性能的能力,但是低成本又如何呢? Yarlagadda承认:“我们正在使用连续的PAN纤维切割成较短的长度。” “但是,市场上有来自Toray,Hexcel,Teijin和其他公司的商业短纤维,以及来自回收和废物流来源的短纤维。 这些纤维没有主要航空航天结构所需的认证,但是有潜力显着降低其他应用的材料成本。”
他继续说:“终,这取决于您的光纤到零件的成本结构。”“使用织物和UD胶带,您要承担从纤维到这种形式再转换为复杂几何形状零件的成本,由于复杂性,缺陷等原因,后者会产生大量的报废和成型风险。 纤维在随后的切割中确实会产生一些额外的成本,但是当我们将其转换为复杂的形状时,它的成型变得非常容易。 因此,避免使用复杂的图案和叠层具有优势,而且在航空航天零件中使用TuFF可以降低成形性并减少废料。”
Hendrix承认UD-CCM可以形成一种深冲部件,这对于使用连续纤维材料的TFF RAPM计划是一个挑战(请参阅即将发布的第2部分)。 TuFF可以使用六张纸而不是20种不同的预成型坯来制造这些零件,这对于实现我们的成本目标至关重要。 他们还证明了他们可以制造传统材料无法制造的几何形状。” Yarlagadda引用了开场照片中所示的华夫格部分:“使用连续纤维是不可能的。 这如何影响您的价值和业务案例计算?这需要你退后一步,问问自己现在该如何制造零部件,以及你可以利用什么样的设计自由度?
?Heider返回到纤维成本,并考虑了另一个因素:废物再利用。 “如果您不需要经过认证的光纤,则可以使用成本更低的短纤或回收光纤。” 大多数回收纤维是短纤维,因为热解和其他一些过程需要切碎,然后才能从废料预浸料和固化的废料/报废部件中除去树脂。 Yarlagadda说:“如果使用短纤维形式作为起点,则所有废料都可以重复使用,从而使您的废品生产过程基本为零。” “这不是DARPA TFF计划的重点,但是我们已经展示了我们可以回收TuFF材料,使该纤维通过TuFF工艺并获得相同的性能。 国防部的应用需要经过认证的航空级光纤,但我们认为短光纤的成本优势仍将使大幅降低成本成为可能。”
下一步
“我们希望完成PEKK和8552的环氧性能测试,然后发布这些结果,以及我们在各种零件成型过程中的工作,” Gillespie说。 “我们有正在申请的,并且正在对该技术进行许可。” DARPA TFF计划于2020年正式结束,并分发了所有测试和结果。
Gillespie说:“初建立TFF时,该程序正在研究为何复合材料没有在国防和汽车领域得到更多使用。” “对于汽车而言,这是因为他们已经投资于金属成型,并且必须对复合材料进行再投资。 但是,当复合材料可以像金属一样成形时会发生什么呢? 然后,重新配置现有的生产流程并利用现有的设备将变得更加容易。”
对于Hendrix而言,紧迫的问题不是大批量生产,而是如何在小批量生产中实现负担得起的重量减轻。 他承认:“我不希望将10,000个铝制零件替换为10,000个复合材料零件,但我要替换几百个。” 为了实现这一目标,下一步是采用一些示例部件,使用这些材料和工艺对其进行演示,这些材料和工艺能够满足航空航天的质量要求,并验证加工铝的经济性。在第2部分中,CW将综述RAPM计划,该计划正在可重新配置的制造单元中探索各种过程,这些过程具有模块化工具以及具有像素化温度控制的快速加热/冷却功能。