
新的非热压罐工艺将树脂传递模塑与预浸料相结合,用于复杂的直升机零件。
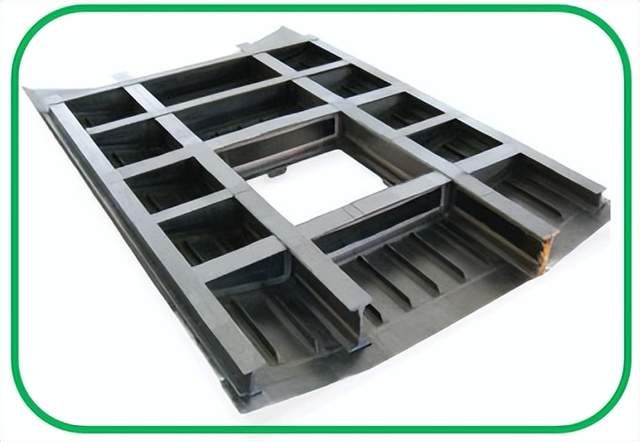
该净形单元化组件由Radius工程公司(犹他州盐湖城)制造,是作为SARAP(可生存可负担可修复机身计划)计划的一部分生产的旋翼机舱顶原型零件。 ~250 lb/~120 kg “格栅加劲”组件的底视图显示了其四根厚的整体纵梁和几个较轻的垂直框架以及整体上蒙皮加劲件。
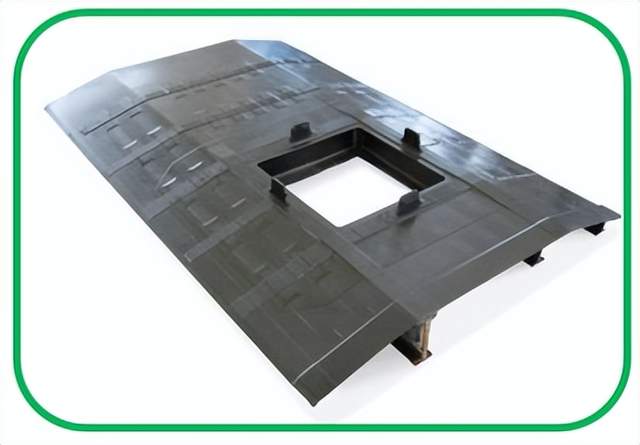
完工舱顶的俯视图显示了整体上蒙皮以及转子变速器的开口和整体支架。舱顶的大致尺寸为9.5英尺×6.2英尺×1英尺(2.9米×1.9米×0.3米),与其他机身部件组合在一起(见第48页照片)。舱顶部分为减少机身部件数量和重量的预期方法建模。
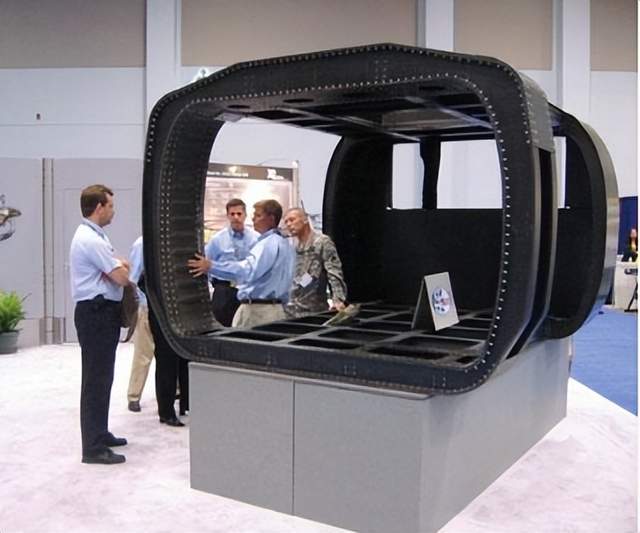
一个完整的SARAP机身原型,在直升机行业的贸易活动展览。SQRTM装配式舱顶组件作为组件的一部分可见,其中还包括其他创新复合材料设计。据报道,西科斯基正在考虑未来直升机制造项目的SQRTM技术。
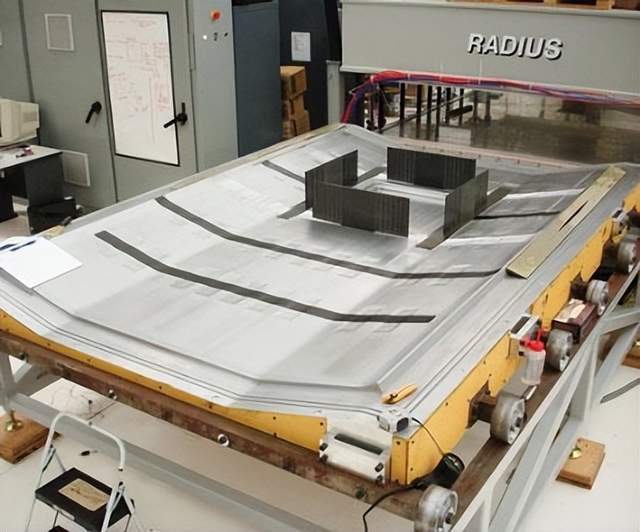
步骤1. 复杂舱顶零件的铺层,如早期阶段所示,包括在下半模上放置去空隙预浸料和干燥预制件(如步骤3所述)的组合。
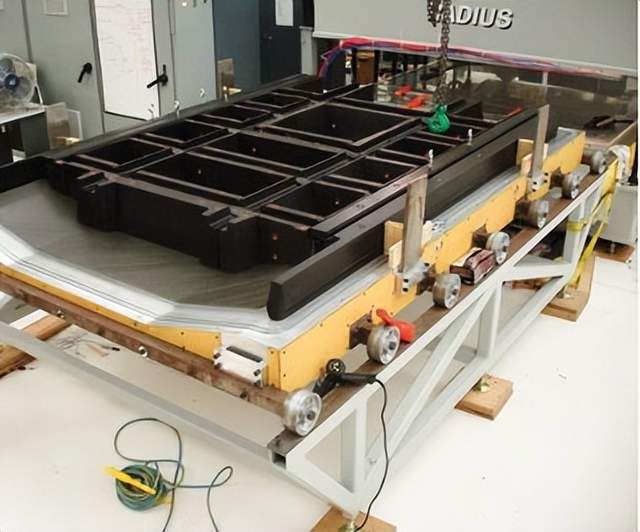
步骤2. 舱顶蒙皮的预浸料铺层已就位,将梁和垂直框架舱顶面的工装嵌块网格已同时就位。
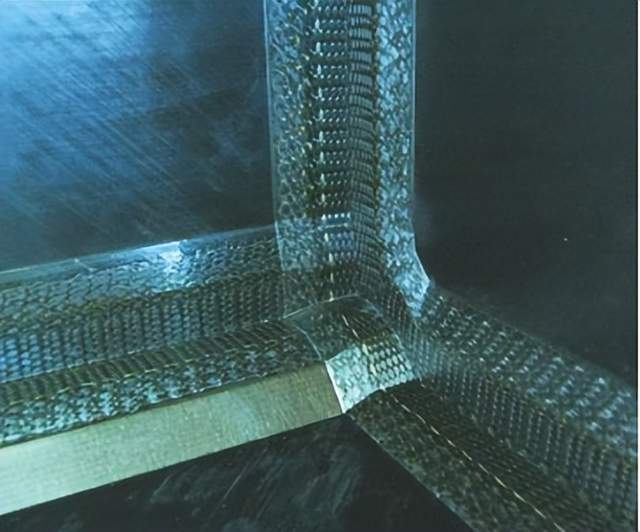
步骤3. 这个特写显示了垂直和水平元素交叉处使用的“pi”预制件。在垂直加劲肋腹板与梁缘条或零件蒙皮相交的任何地方,pi预制件的两个支
腿形成一个槽,接受腹板,而垂直预制件元件平放在水平梁缘条或蒙皮上。预制件用于填充腹板和盖或缘条之间的半径,用于零件的许多梁和框架。
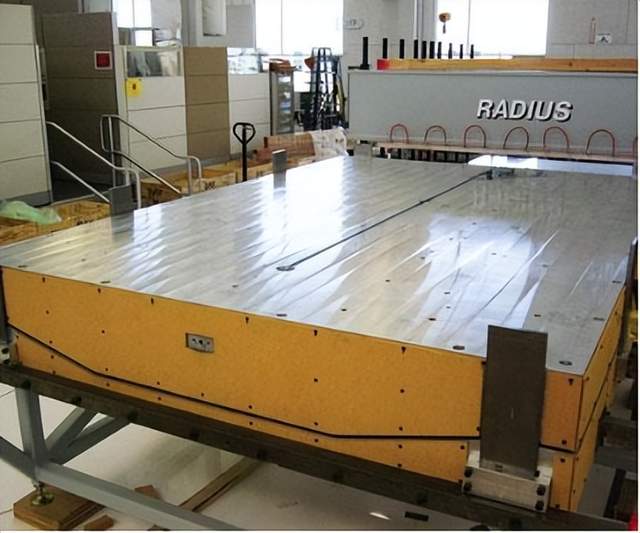
步骤4. 已完成铺层,已安装多个工具镶块,并关闭模具。此时,使用与预浸料相同的树脂进行注射,以保持模具内稳定的静水压力。
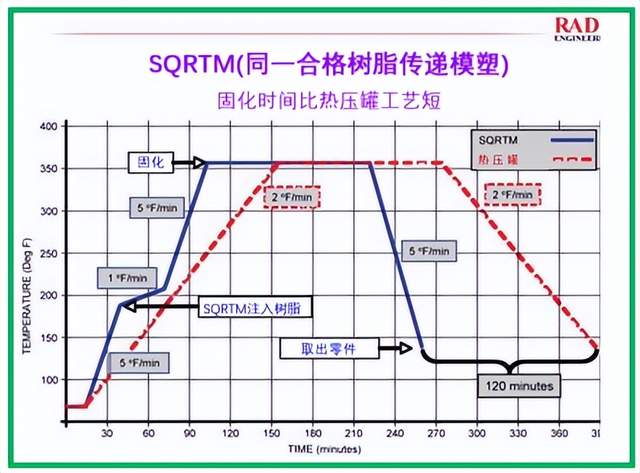
步骤5. 注射后,开始治疗。如图所示,SQRTM能够实现更快的加工,因为压机和工具的更大导热系数允许更快的加热和冷却。RTM固化比热压罐循环短两小时。
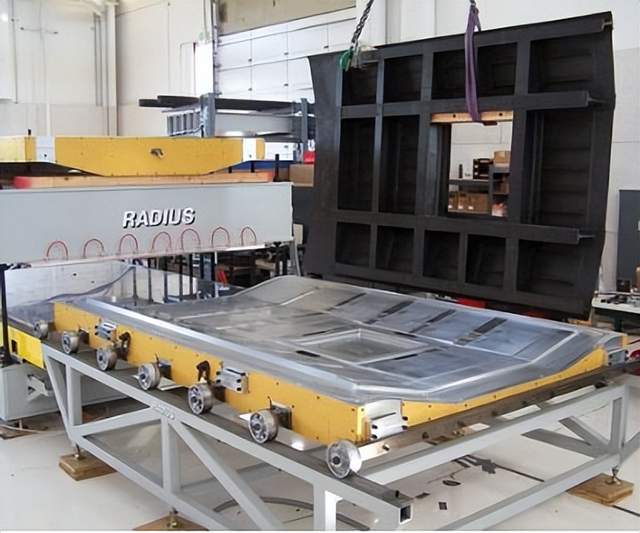
步骤6. 固化的舱顶部件从工具底座提起时显示。工具左侧可见加热压板压力机,带有焊接钢上下衬垫,磨平至高公差,用于加热和夹紧工具。
目前,非热压罐(OOA-out-of-autoclave)加工的趋势是由制造商生产更大零件以帮助降低制造成本的竞争需求驱动的。尽管在过去几年中引入了许多OOA材料和方法,但很少有超过SQRTM的优雅,SQRTM是同一合格树脂传递模塑的缩写。SQRTM由Radius Engineering Inc.(犹他州盐湖城)开发,目前正在商业化过程中。SQRTM是一种封闭成型方法,将预浸料加工和液体成型相结合,以生产真正的净形状、高度统一的航空航天零件。简言之,SQRTM设计用于在不使用热压罐的情况下生产热压罐质量零件。
Radius工程公司总裁米特里耶·米洛维奇说:“在过去几年中,复合材料航空航天部件的规模和复杂性显著增加。”。“我们设计了一种可行的替代方案,在复制合格热压罐工艺的同时提供显著优势。”SQRTM方法已成功应用于多个航空航天项目,包括RQ-1B全球鹰无人机(UAV)的翼尖扩展。但迄今为止,最艰难的测试是一个极其复杂的整体式原型直升机座舱顶部,它是根据可生存可负担可修复机身计划(SARAP-Survivable Affordable Repairable Airframe Program )生产的,SARAP是西科斯基飞机(康涅狄格州斯特拉特福德)和美国陆军航空应用技术理事会(AATD,Ft.Eustis,Va.)之间的合作协议。SARAP机身的创新设计和制造(SQRTM装配式舱顶是其中的一个组成部分)实现了积极的重量减轻和成本降低目标。在座舱顶部的成功工作帮助SARAP虚拟样机和验证开发团队赢得了美国国际直升机协会2008年的Robert L.Pinckney奖(以表彰杰出的波音制造工程师命名),该奖项表彰了垂直飞行飞机或组件制造研发方面的显著成就。
液态模塑+预浸料
SQRTM与标准树脂传递模塑(RTM)的区别在于,它代替了干纤维预制件,代替了预浸料铺层。预浸料层布置在模具内,模具关闭,然后,有点违反直觉,液体树脂注入到工具中。米洛维奇说:“这使得该工艺类似于让热压罐工艺。”他指出,注入的树脂与预浸料中使用的树脂相同,因此,采用该工艺的人无需重新鉴定材料。
工具内精密设计的浇口和通道有助于在注射前从叠层中排出空气,并使注射的树脂能够在约100 psi/6.89 bar的均匀流体压力下沿整个零件边缘填充所有空腔。“树脂不是用来浸渍预浸料的,”米洛维奇解释说,“只是为了在模具内保持一个稳定的静水压力。这个压力保持挥发物和水蒸气在溶液中,以防止空洞的形成。”
事实上,传统的热压罐工艺有时使用高温橡胶边缘挡块或其他材料作为叠层和装袋的一部分,以防止树脂在热压罐压力下从预浸料中逸出——如果有足够的树脂挤出,层压静水压下降,叠层内树脂中逸出的任何空气或挥发物都会产生空隙。然后,在SQRTM工艺中,注入的加压树脂起到“流体坝”的作用,防止树脂挤出,同时复制固化过程中热压罐的固化压力。
Radius业务开发负责人汤姆·考林声称:“使用SQRTM比使用热压罐更容易控制层压质量,因为树脂静水压力直接由树脂注射器控制,而不是取决于热压罐容器内的变量和袋下层压。”
为了适应其SQRTM工艺,Radius设计并制造了一个大型压盘系统,该系统配备了高公差的焊接钢磨平的上下支撑。当加载的双面工具放置在压力机内时,下部靠垫由一系列类似于消防软管的气囊支撑。
米洛维奇指出,在注射之前,袋子被充气,迫使下摇枕向上靠着工具和上摇枕,以优化夹紧力。
考夫林说,上部和下部的垫子都是电加热和水冷的,在治疗过程中可以调节温度。“如果一个工具有一个可变质量,根据零件配置,一个区域比另一个区域厚,”他解释说,“分区加热允许压机在完成工具的完整热分布后,在较厚的区域施加更多的热量,以便零件始终看到一致的热循环。”
SQRTM与RTM类似,在工具上抽真空并加热压力机和工具。然而,对于SQRTM,在热压罐条件下,以与预浸料相同的升温速率进行加热,并通过过程控制器注入树脂,该控制器还监控和调整压力机温度。另外,SQRTM工艺的独特之处在于所使用的真空度,考夫林补充道,并指出Radius开发的真空泵可产生<0.5 mm/Hg的真空度,这“比标准车间泵所能产生的真空度更高”.
由于压机和工具的较高热导率允许更快的加热和冷却,因此SQRTM固化周期可比高压釜周期短两个小时。
与传统RTM相比还有其他优点。零件厚度由匹配的工装控制,避免了真空装袋过程中固有的潜在厚度变化。从完全浸渍、合格、增韧预浸料开始,消除了注射过程中出现干点的风险,并且需要通过液体树脂将增韧剂引入零件。此外,由于该工艺严格遵循使用先前合格材料的标准热压罐处理步骤,因此对客户来说风险更小,舒适度更高。尽管这种工艺在某种程度上更适合平面型零件,米洛维奇说,SARAP舱室的舱顶表明,非常大的规模,复杂的零件在其范围内。
网格加筋零件的净形状
“我们的重点是净形状的部分,”米洛维奇说。“我们正在寻找集成多个零件的方法,以减少装配劳动、降低成本和重量。”这一理念推动了SARAP项目SQRTM的开发,该项目侧重于寻找创新方法,以减少结构重量和紧固件数量,并提高旋翼机零件的损伤容限。除了Radius,SARAP团队还包括Automated Dynamics(纽约州斯克内克塔迪)和GKN Aerospace Services Alabama(阿拉巴马州塔拉塞市)。Automated Dynamics制造了热塑性复合材料下机身组件,GKN制造了机身框架、侧蒙皮和后舱壁,并组装了最终的SARAP技术验证组件。
为了制舱屋顶组件,预浸料首先被切割成型,以形成大部分零件。舱顶组件中使用的预浸料为氰特的Cytec 5250-4,该预浸料是由于其与Cytec的5250-4液体RTM树脂具有固有的化学兼容性而选择的。
预浸/注射树脂匹配是SARAP舱顶制品的一个重要考虑因素,因为典型的SQRTM工艺有所改变,包括一些干纺织材料的灌注以及预浸料。西科斯基的机身开发项目负责人汤姆·卡斯滕森指出,使用相同的基础树脂系统消除了对树脂混合和可能导致的机械性能潜在变化的担忧。
配套的单向碳/环氧胶带和机织物预浸料在工具外部单独去胶,以去除任何截留的空气或树脂浓度的局部区域-通常为材料规定的步骤。根据材料规范,将切割层铺在加热的平模胎板或工作台上,装袋并置于真空下。11层预浸料堆在达到基于所需减粘水平的最高温度后约1小时内减粘。然后将去毛刺的铺层或“书本”转移到工具上,开始铺层,这一过程需要两名技术人员将近两周的时间才能完成。
在铺层过程中,预浸料形成零件的腹板和凸缘。这些由编织的三维干燥“π”预制件连接,因其与希腊字母π相似而得名。这些预制件由Bally Ribbon Mills和Albany Engineered Composites制造。在垂直加劲肋腹板与梁翼缘或零件蒙皮接触的任何地方,pi预制件的两个支腿形成一个槽,接受腹板,而垂直预制件元件平放在水平翼缘或蒙皮上。预制件的作用是填充腹板和每个零件的众多梁和框架的盖或法兰之间的半径,提供所需的刚度和强度。
米洛维奇说,随着工具的组装,精密加工的工具嵌入件和细节压缩并整合了每个预制件细节,形成了“净斜边”。在三向交叉处,在插入工具以形成斜接接头之前,对预制件进行手工切割。“我们开发了斜接预成型交叉点的方法,以创建干净和功能性的接头。最大的好处是消除了边缘修整的需要,并且在固化后大大减少了后续零件加工。”
连接仪器并在工具上抽真空后,以热压罐规定的升温速率加热压力机,并在升温过程中停留期间注入树脂。注射大约需要45分钟,固化大约需要4小时。米洛维奇说,通过在低于固化温度约70°F(21°C)的情况下,在工具仍然热的情况下脱模零件,可以缓解铝工具的热膨胀系数问题。
从原型到方案
迄今为止,已成功使用SQRTM生产了三个舱顶组件。由于匹配工具的严格公差,零件上的所有表面显示严格的尺寸控制,在±0.005英寸(±0.125 mm)范围内。固化后只需对梁的边缘和端部进行微调。因此,西科斯基正在考虑未来升级美国陆军UH-60直升机平台的技术,并计划在其他项目中评估该技术。
西科斯基不是唯一对SQRTM感兴趣的航空制造商。波音公司最近发布了涵盖SQRTM工艺的工艺规范,使用BMS-8-276增韧预浸料进行封闭成型。Radius报告称,波音公司及其至少一家一级供应商已经对通过SQRTM制造的面板、子元件和全尺寸零件进行了测试,发现其与热压罐处理相当。米洛维奇总结道:“它正在被接受,并将引领其他应用程序将多个零件集成到一个组件中,从而节省大量资源。”。
编者按:可生存可负担可修复机身计划由航空应用技术理事会和西科斯基飞机公司根据第DAAH10-03-2-0003号技术投资协议提供部分资金。使用此信息并不意味着得到美国政府或陆军部的认可。
编后语
昨天发了一篇《客舱无窗户的公务机 -幻影3500》,很快就有同仁回微信表示,对此工艺感兴趣。其中原昌飞负责复材龙国荣副总,希望进一步了解细节。为此,将2010年一篇旧文,编译出来,供同仁们学习、参考!
原文,《SQRTM enables net-shape parts》 2010.8.31
杨超凡 2025.7.1